Biological engineering, or bioengineering, is a science-based discipline founded upon the biological sciences in the same way that chemical engineering, electrical engineering, and mechanical engineering are grounded in chemistry, electricity and magnetism, and classical mechanics, respectively.
Bioengineering is an exciting and rapidly evolving field focused on creating sustainable, eco-friendly, and innovative materials for vehicle interiors.
Bioengineering includes the likes of:
- biopolymers, which are biodegradable materials derived from renewable sources like plants. They are being used in various car interior components such as dashboards, door panels, and seat covers. Biopolymers help reduce the reliance on petroleum-based plastics and lower the overall carbon footprint of vehicles.
- natural fibers from sources like bamboo, hemp, organic cotton, mushrooms, and more are being used for upholstery and other interior components. These materials are sustainable, and provide a natural, different, and sometimes luxurious feel.
Why Bioengineering?
Petroleum-based polymers are widely used in the automobile and aviation industries. Traditional car interiors are filled with plastic components that contribute to long-term waste and pollution. This, and their lack of biodegradabilit are leading researchers to look (nudged along by increasingly stringent environmental regulations) for more ecologically-compatible biopolymers and biocomposites. Biopolymers have potential applications in various exterior and interior parts of an automobile, including steering, doors, wheels, electrical components, engine parts, exhaust systems, and so on.
Interior Bioengineering and Sustainability
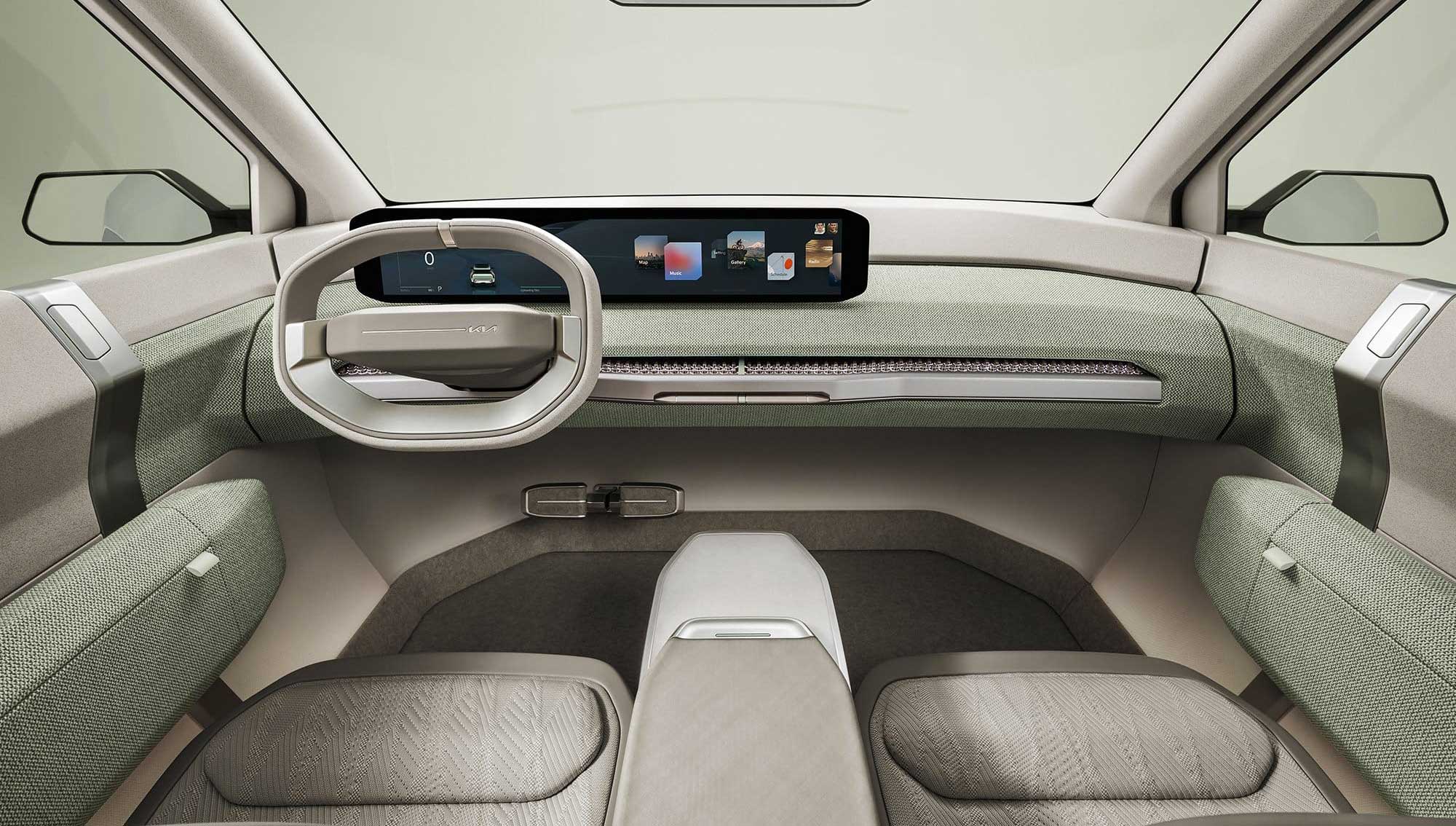
According to the study « Engineering biology: The time is now » by the Capgemini Research Institute on the bioeconomy, over 70 per cent of companies expect to be able to achieve their sustainability goals much faster with the help of biosolutions. Other motives include cost reduction, product optimization and—especially in Europe—greater safety of product and production processes.
According to Felizitas Graeber, Managing Director of Capgemini Invent in Germany, biotechnology enables innovations that « can be found in all sectors of industry—from energy and utilities to the automotive industry, healthcare and agriculture ».
The study found that almost all managers surveyed (99 per cent internationally, 100 per cent in Germany) expect bioengineering to bring about major changes in their industry in the next two to ten years and beyond. In Germany, 58 per cent expect this to happen in the next two to five years, and most organizations in the industry (96 per cent internationally, 99 per cent in Germany) are already working on biosolutions: 40 per cent were in the exploration phase, for example; 56 per cent were conducting research and pilot projects or using biosolutions on a commercial scale. Most organizations are planning to increase investment in biotechnology.
According to the study, fields of application for bioengineering have become established in the automotive industry; interior is at the top of the list, with bioplastics and leather alternatives for interior parts (seats, trim, floor, and trunk). In automotive, it also includes bio-based paints and coatings, bio-based alternatives for battery materials and battery recycling, and biofuels.
Respondents saw digital and engineering technologies as key factors in reducing costs, optimizing bioprocesses, shortening time-to-market for biosolutions and mitigating environmental and social risks. They rated AI as the technology with the greatest transformation potential. Robotics for process automation and digital twins of bioreactors that predict production results were also named as important measures for reducing costs and scaling up more quickly.
It Started Long Ago:
Toyota Sai, 2010
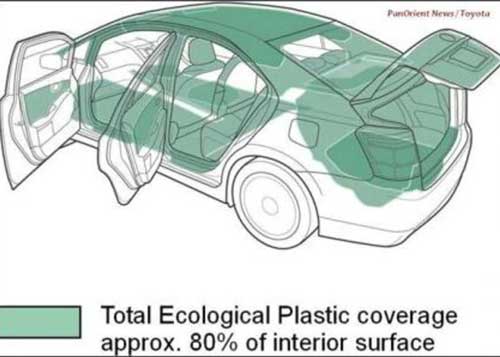

Toyota has been at the forefront of bioplastic innovation, incorporating plant-based materials into the interiors of several of its models, starting with the Toyota ‘Sai’ Interior, back in 2010. By replacing petroleum-based plastics with bioplastics, automakers can significantly reduce the carbon footprint of their vehicles, all while offering drivers a sustainable, high-performance product and experience that doesn’t sacrifice style or comfort.
At Tokyo 2019 Motor Show, a Japanese consortium proposed wooden cars made of plant-based cellulose nanofibers.
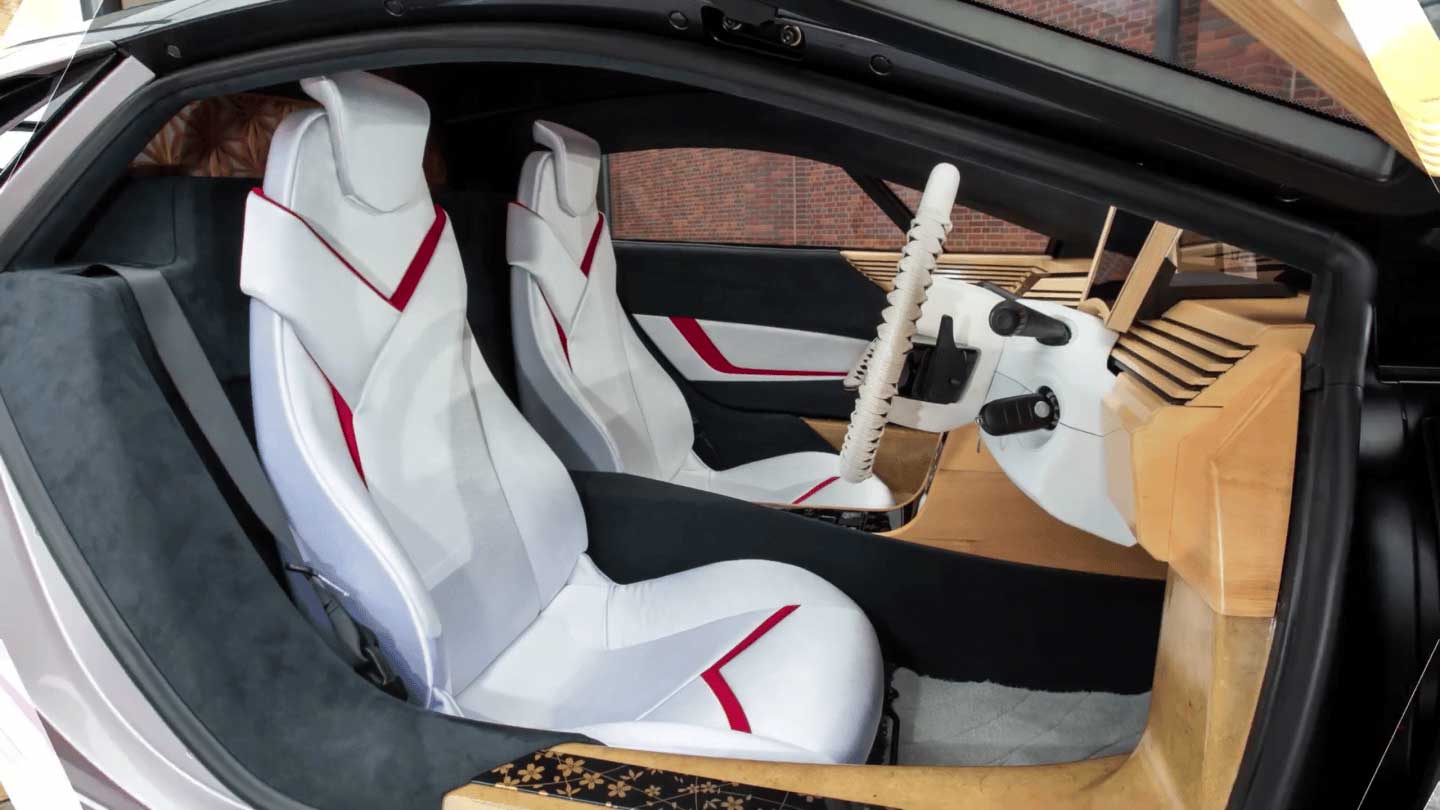
Called the Nanocellulose Vehicle, or NCV, it was said to reduce weight by around 10 per cent compared to a car built from standard materials, thus saving about one person’s worth of household carbon emissions for a year.
Made essentially from wood chipped, pulped and boiled in chemicals to remove lignin and hemicellulose, it’s a highly condensed, lightweight and incredibly strong material that’s also very recyclable.
Reutlingen University inBiO Project, 2019
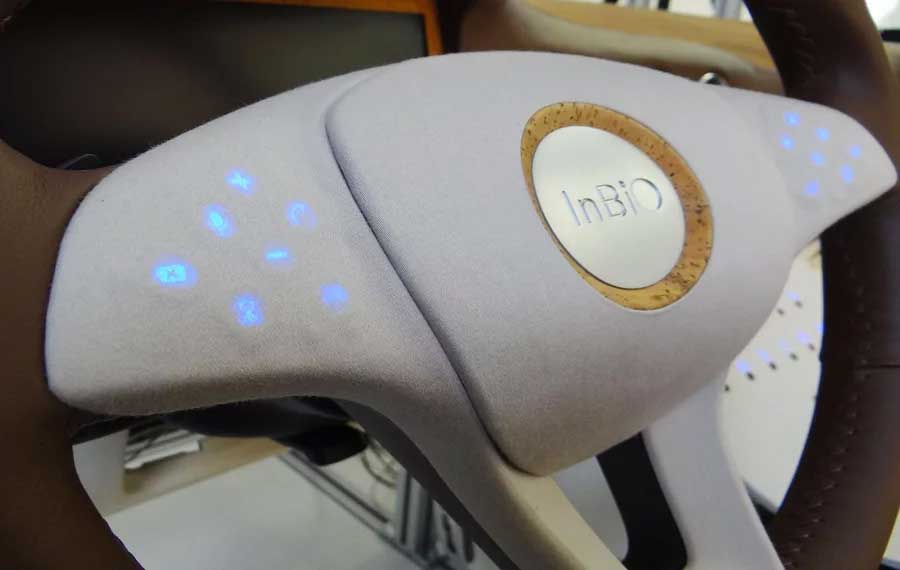
The aim was to develop and realize a concept for an innovative, sustainable, and user-friendly interior. As one element of the project, trim components made of bio-based materials such as cotton and wood were developed. An overall goal was to design a user-friendly interface, that reduces complexity without reducing functions. The bio-based materials integrate control and feedback functions that can be easily implemented in common CAN-bus systems used by the automotive industry. Four materials were chosen after balancing the material properties and the identified customer expectations. These materials were cottoning fabric, cork, leather, and a product called Nuo, which is a veneer laminated to a textile fabric before it is laser-cut.
Automaker & supplier examples
BMW
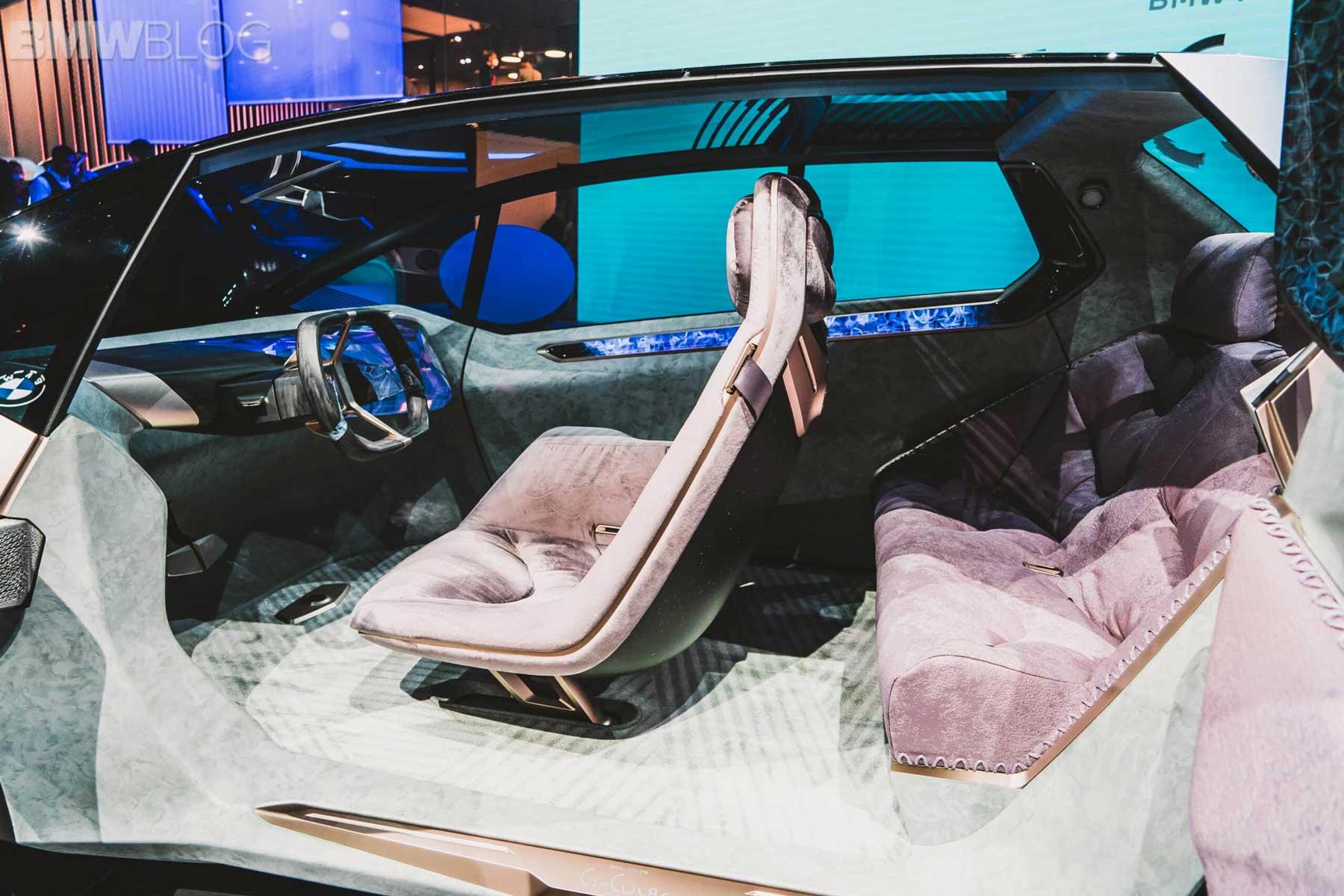
In 2021, BMW stated they’d decided to give preference to ‘secondary materials’ for future vehicles within the framework of selected product, material and supplier requirements, holding them to the same standards of quality, safety and reliability as ‘primary materials’. The BMW i Vision Circular was emblematic of this approach. The vision vehicle is made from recycled materials and renewable raw materials, among other things.
Vehicles with vegan interiors have been available from the BMW Group since 2023, thanks to innovative materials with leatherlike properties. In future, these can also be used for the surfaces of steering wheels, where they must meet particularly high requirements in terms of feel, appearance and wear resistance. According to BMW, the new material for the steering wheel surfaces saves around 85 per cent of CO2e emissions along the value chain, compared to leather. BMW also sees a further opportunity to reduce the CO2e footprint in the supply chain in the increased
GM
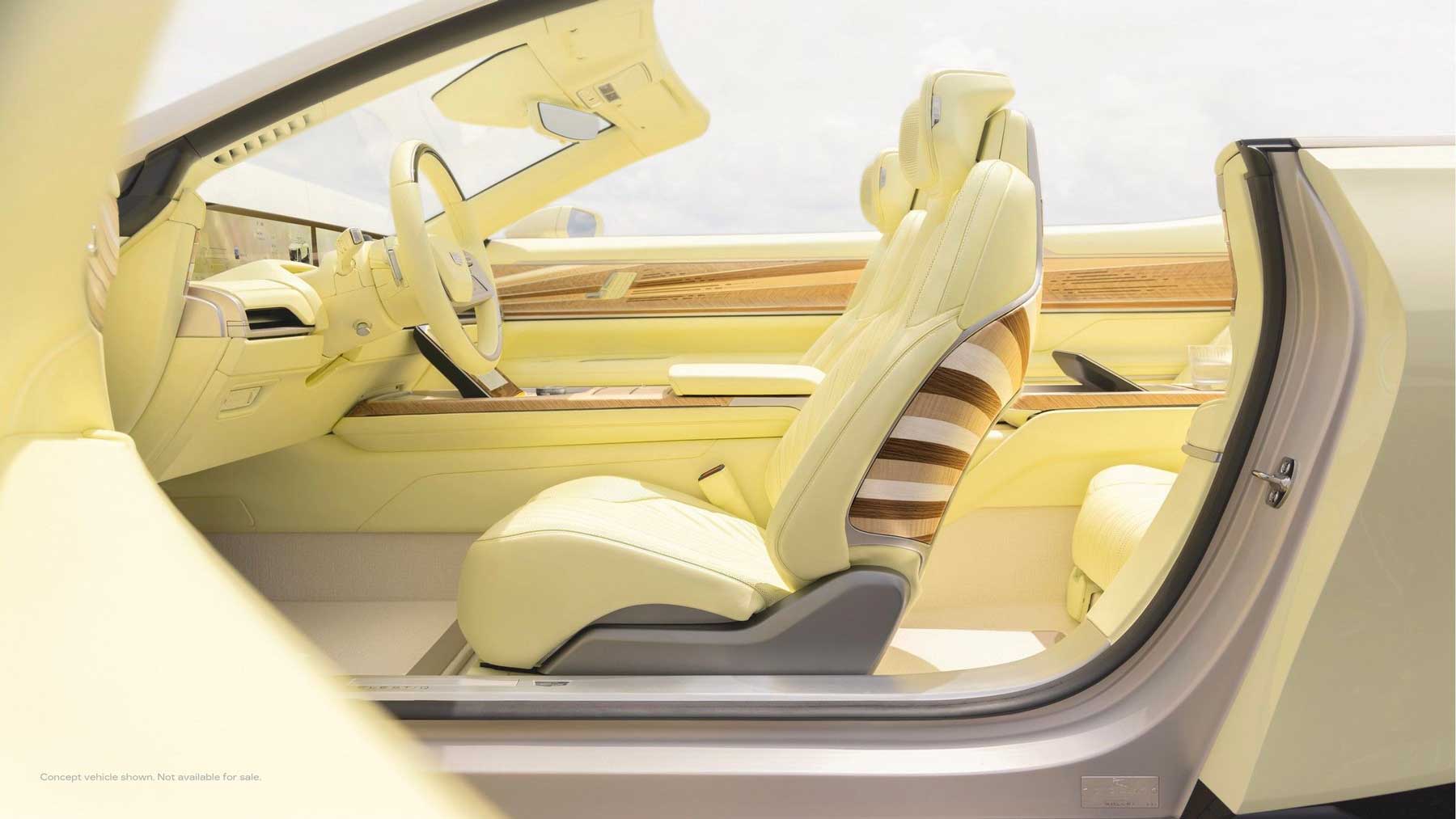
Biomaterials company MycoWorks and General Motors unveiled a concept car featuring mycelium bio-based materials, developed through a partnership established in 2022. The concept electric vehicle, caled the Cadillac Sollei, integrates MycoWorks’ Fine Mycelium in an iridescent form within the charging mats on the console and door map pockets.
Volvo
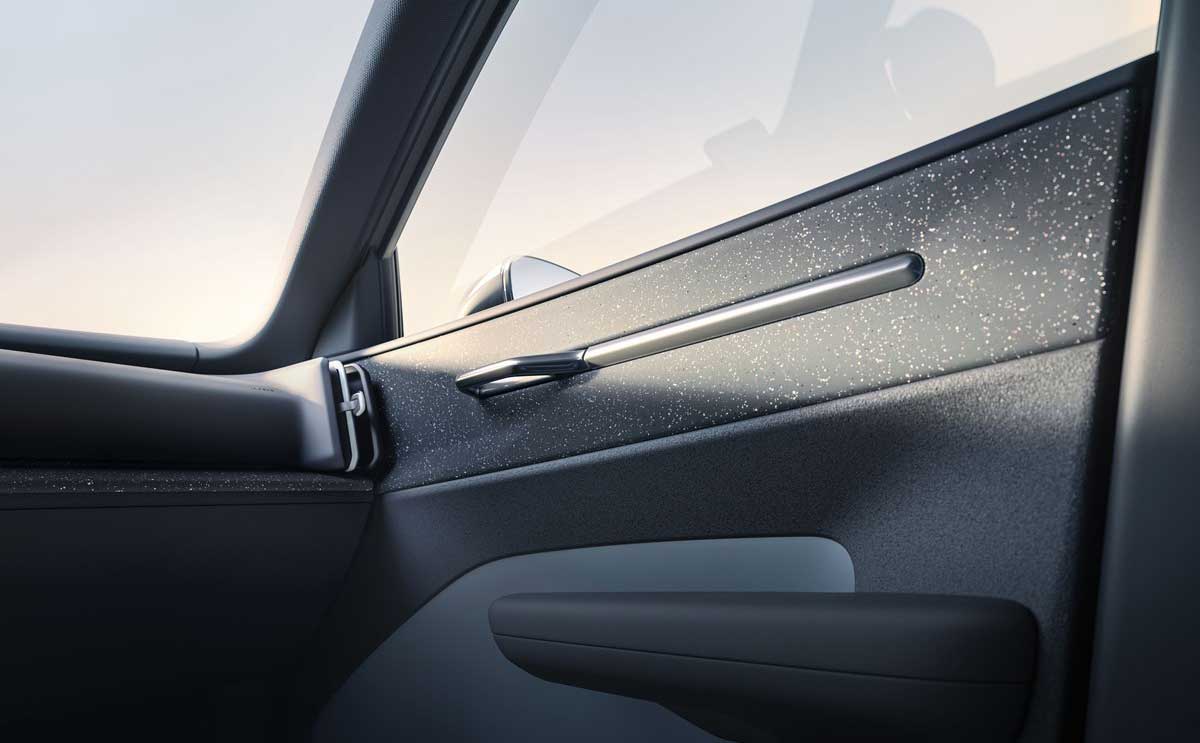
The EX30 marks a major step for Volvo and Alliance member Bcomp, as customers can now select two interior trim packages featuring the natural aesthetics of woven ampliTex flax fibers. The compact SUV focuses on sustainability and is designed to have the lowest carbon footprint of any model in Volvo Cars’ history, with Bcomp’s flax fiber composites now offered as an optional trim for the dashboard and doors.
Mercedes
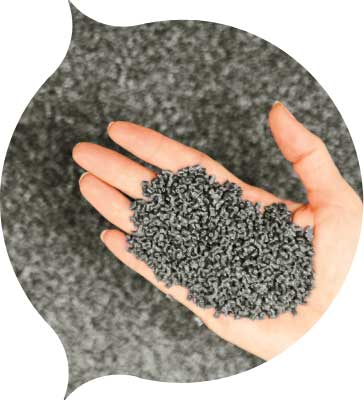
Mercedes-Benz’s sustainable business strategy calls for reducing fleet consumption through lightweight construction. The Mercedes Vision EQXX electric concept uses a fully bio-based material developed by UBQ Materials and made from organic and unrecyclable household waste. UBQ is used in the ‘bionic’ structure of the vehicle’s body shell and in interior structures such as the headrests.
Israel-based UBQ Materials focuses on closing the loop between the ecosystems of waste and materials. Their bio-based UBQ thermoplastic is made entirely from residual waste, including organics and hard-to-recycle materials. The company is expanding globally, working to provide the world’s largest businesses, municipalities, and consumers with a climate-positive solution for a circular economy.
Sherpa
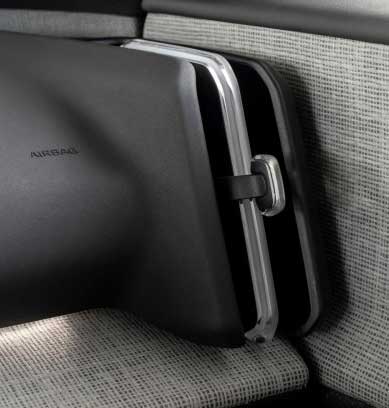
Greenlander, in partnership with investor and flax material specialist Depestele, showcased the Sherpa, which they describe as ‘the ultimate 4×4 expedition vehicle’ built to leave less impact as it travels, at JEC World Paris this year; see video. The Sherpa, formally launched at the Caravan Salon in Dusseldorf this summer, combines plant-based fibers like flax with bio-based resins and sustainable core materials like cork, wood and recycled PET foam to create durable and lightweight components. As well as the low impact materials, Greenlander also provides a unique business model, offering the composites items as a service and taking them back at the end of their life where they can
Covestro + Beyond Leather
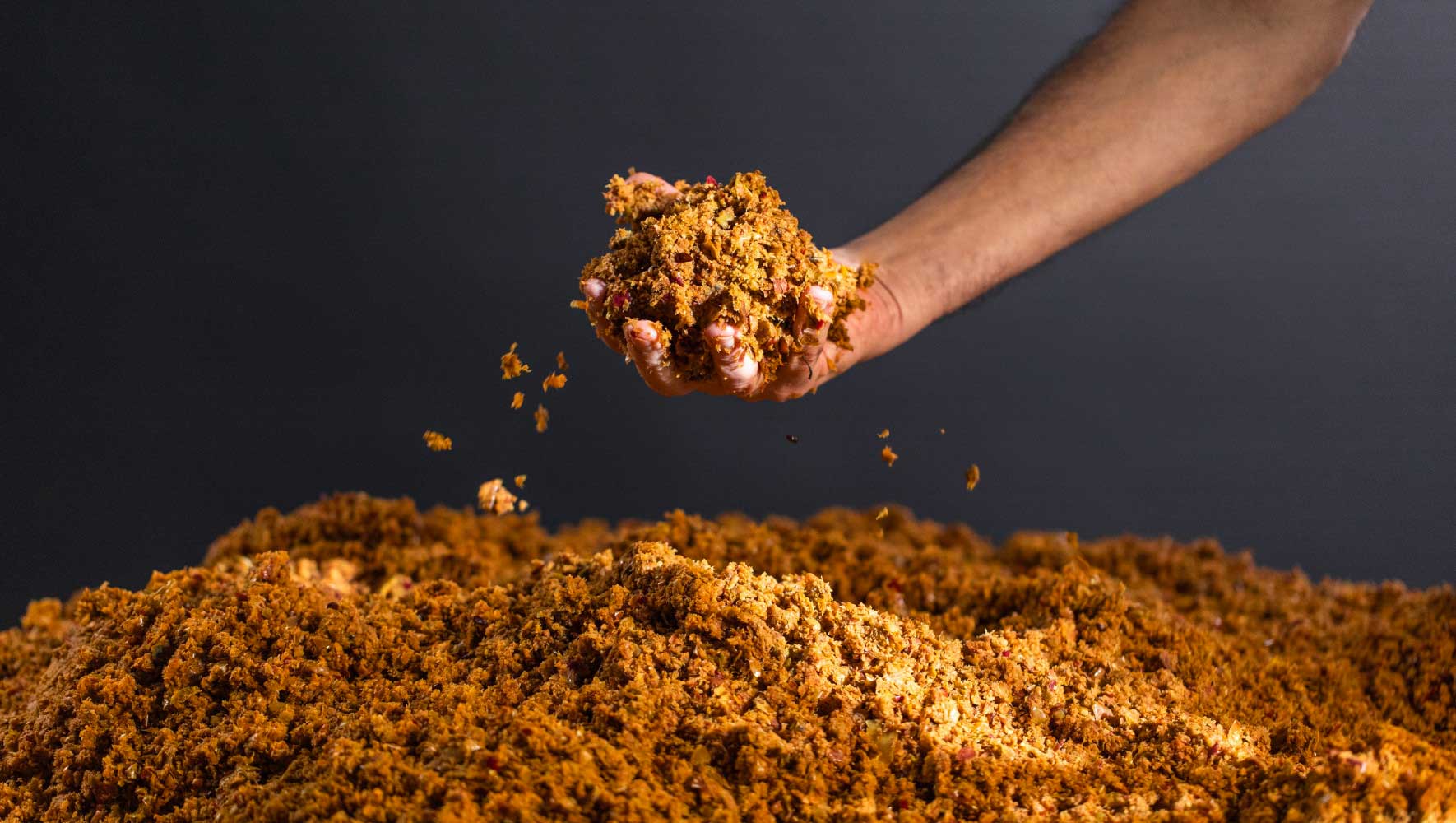
Covestro has partnered with Beyond Leather Materials to develop Leap, a bio-based leather alternative. It contains 85 per cent biomaterials, and is made using apple waste generated from juice and cider manufacturing.
Leap uses Insqin technology based on polyurethane dispersions made with partially bio-based content. Around four million tons of apple waste is produced every year, and Beyond Leather’s approach reuses this waste to make a leather alternative.
Apple waste contains high content of short fibers and polymers, which can be activated to give a strength and suppleness to the final material, recreating the functional and aesthetic properties of leather. The waste blend is applied to a Tencel textile backing and finished with the protective coating containing Insqin to make Leap.
Forvia Materi’Act NafiLean
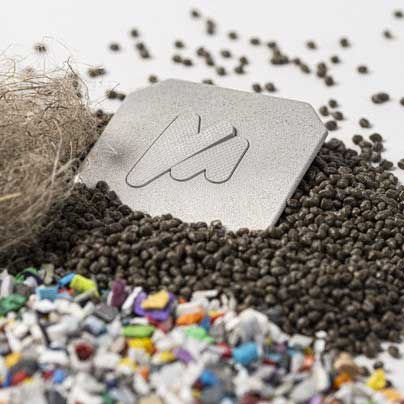
Forvia Materi’Act NafiLean is a 100-per-cent recyclable biocomposite materials, NafiILean-R is a blend of 20 per cent natural hemp fibers recycled polypropylene, delivering a 73-per-cent CO2 reduction and cutting weight by 20 per cent. This product is a finalist for the 2025 Automotive News PACE Awards.
Aimplas Forest project
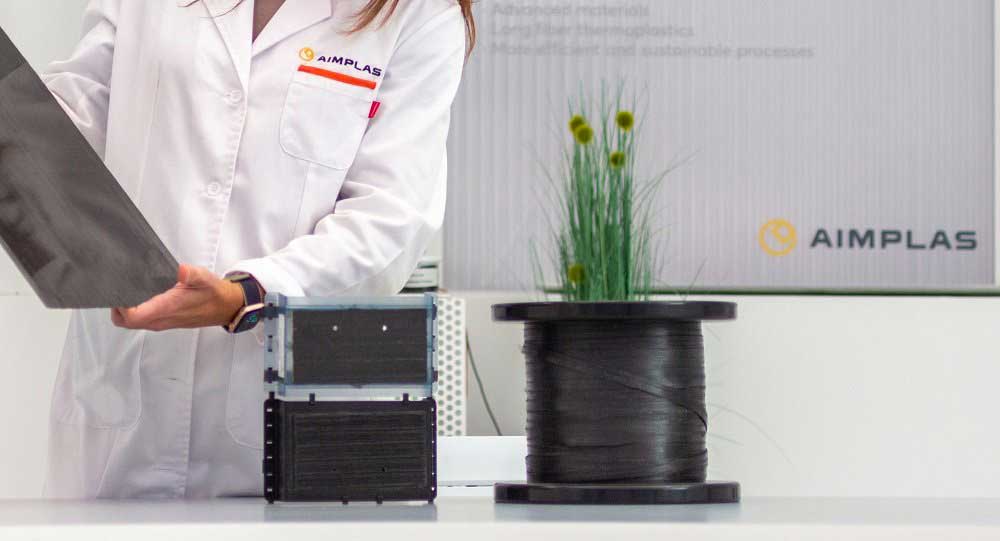
Aimplas, the Plastics Technology Centre (Valencia, Spain) leads an EU-funded research project on advanced lightweight bio-based or recycled materials to facilitate the decarbonization of the transport sector. The project consortium comprises 14 partners from eight countries, developing innovative bio-based polymers & additives and recycled carbon fibers for sustainable and safe transport applications.
These biocomposite candidates will be obtained using one-shot manufacturing techniques, involving Out-of-Autoclave (OoA) processes to build and test prototypes with improved multifunctional properties (mechanical resistance, fire-retardant, EMI-shielding) for transport application
Value chain analysis is crucial for every involved business to develop the eco-system, and to gain an understanding of the material availability, costs, benefits, and everything to support reliable automotive mass production.
The Torino DVN-I workshop in front of us is a great opportunity to keep the discussion going. Program docket and registration are available online.