There’s been a lot of exciting progress in the use of sustainable and circular materials for car interiors recently! Here are some highlights coming directly from automakers:
Foam in Fords
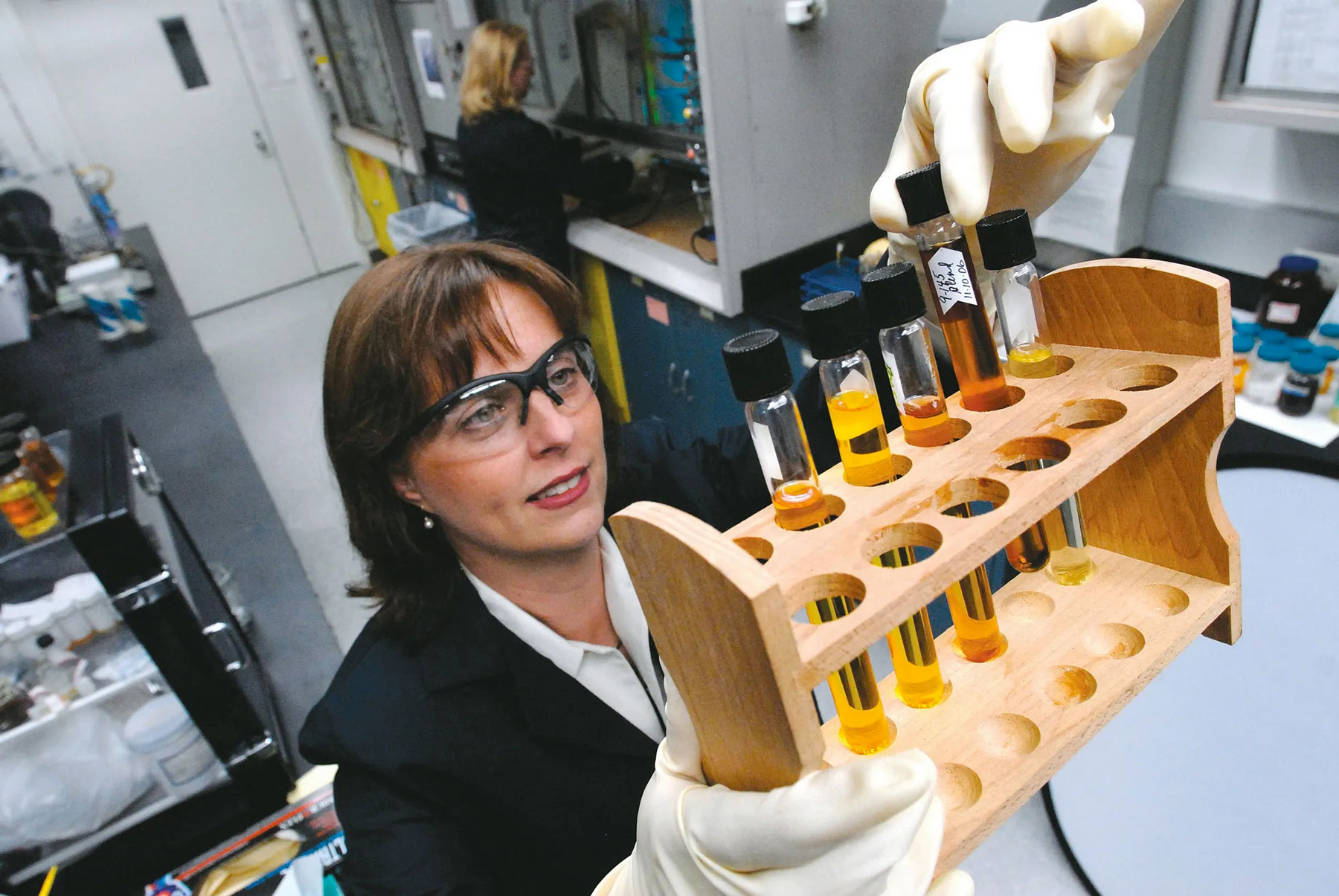
Ford was the first automaker to formulate and test new seat foam and plastic components using carbon dioxide as a feedstock. With up to 50 per cent CO2-based polyols, the foam is meets rigorous test standards. CO2-derived, more sustainable foam will reduce the use of fossil fuels.
Ford also uses soy-based foam, developed in their biomaterials lab in Dearborn, Michigan. It first appeared in the 2008 Mustang, and has since been incorporated into every Ford and Lincoln seat cushion in the U.S; the eco-friendlier material has also been made available to other automakers.
GM and cardboard
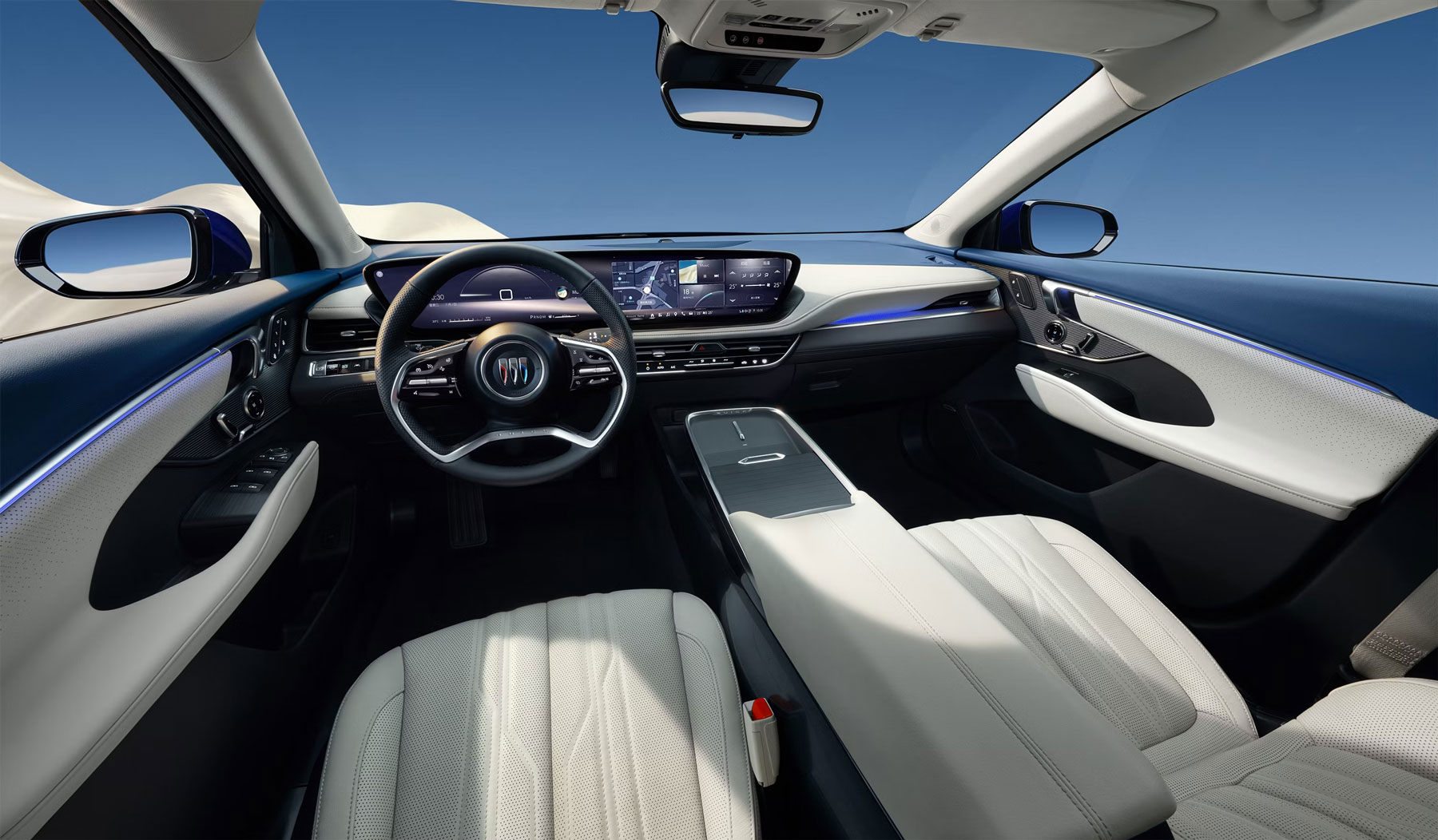
General Motors’ recycling project is using soundproofing material made from recycled cardboard packaging from parts suppliers, including a proprietary blend of wood pulp for fiber headliners in the Buick LaCrosse and Verano.
Toyota and sugarcane
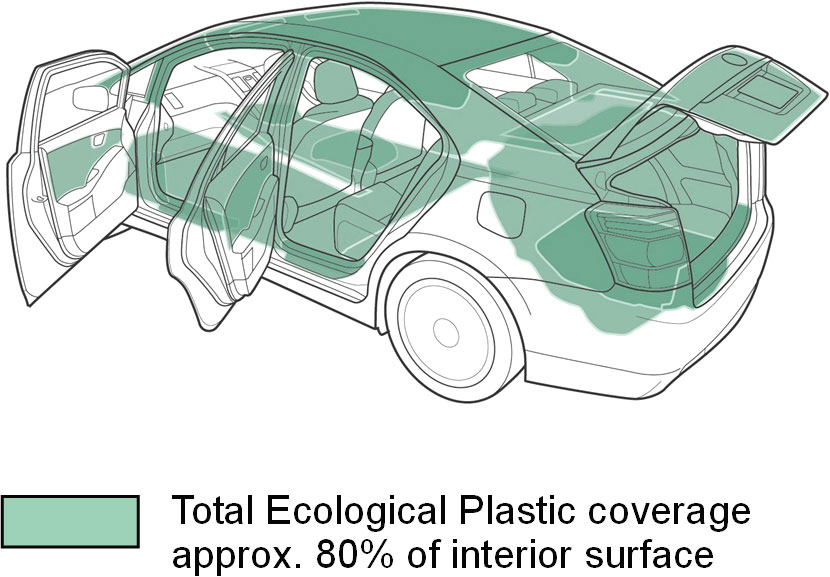
Toyota makes seat cushions, radiator tanks, and other components from bioplastics that use glycol from renewable sugarcane instead of from petroleum.
More examples from recent years
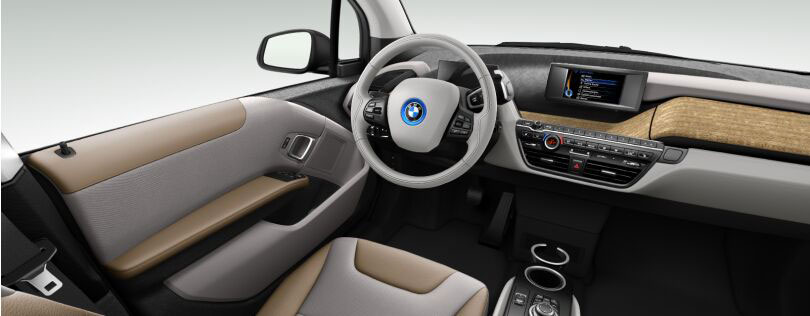
- BMW puts sustainably-grown eucalyptus wood into the dashboard of the electric i3. They also use plant-fiber-reinforced material in door cladding, and recycled plastic fabric seat covers.
- The Audi A3 has cotton fiber in the floor insulation, recycled paper in the cargo area floor, and cellulose in the headliner.
- The Chrysler 300 has recycled plastic in the console and center stack.
- The Dodge Dart used fabric from recycled denim jeans in the trunk liner.
- The Honda Accord Hybrid and Plug-In Hybrid have a proprietary biofabric in the seat covers.
- The Hyundai Elantra and Kia Rio have soy-based foam seat cushions.
- The Jeep Wrangler has recycled plastic in the underbody shields and wheelwell liners.
- The Kia Soul EV has cane- and cellulose-based bioplastics in the door panels, headliner, seat fabric, roof pillars, and carpeting.
- The Lincoln MKX has plastic reinforced by cellulose from sustainably-grown trees replacing fiberglass in the center console.
- The Lexus RX 450h uses bioplastics in its seat cushions.
- The Nissan Leaf has recycled soft drink and water bottles in the seat cover fabric, and recycled jeans and other cloth in sound-deadening panels.
- The Toyota Corolla has bioplastics in the seat cushions.
- The Volkswagen Golf uses cotton fiber in the floor insulation, recycled paper in the cargo area floor, and hemp and flax fiber in the door panel trim.
- Mercedes’ Dinamica microfiber is a synthetic suede that looks great and offers exceptional grip on steering wheels, seats, and other high-touch surfaces; it is made from recycled bottles. Floor coverings contain Econyl, which includes recycled nylon waste from old fishing nets and carpet remnants. It also uses Karuun, an innovative compressed timber product that grows very fast and is harvested by hand in Indonesia.
And this list could go on and on! Sustainable, recycled interiors are just one element of more sustainable motoring. But as something we feel, touch, and see daily, it sounds consistent with the industry efforts trying to minimize overall impact of mobility on the planet.
Mercedes
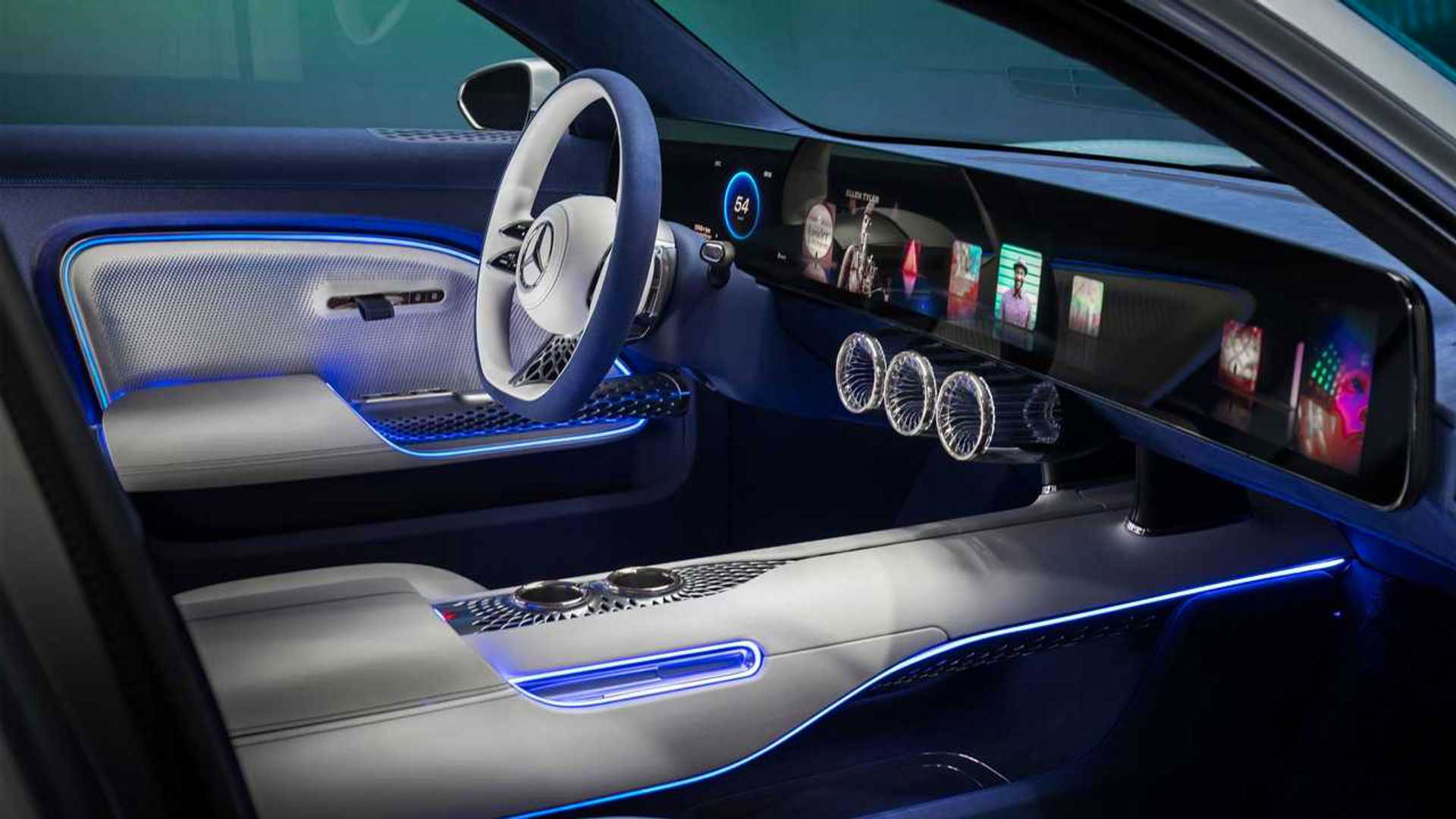
Mercedes-Benz’s sustainable business strategy calls for reducing fleet consumption through lightweight construction. The Mercedes Vision EQXX electric concept uses a fully bio-based material developed by UBQ Materials and made from organic and unrecyclable household waste. UBQ is used in the ‘bionic’ structure of the vehicle’s body shell and in interior structures such as the headrests.
Israel-based UBQ Materials focuses on closing the loop between the ecosystems of waste and materials. Their bio-based UBQ thermoplastic is made entirely from residual waste, including organics and hard-to-recycle materials. The company is expanding globally, working to provide the world’s largest businesses, municipalities, and consumers with a climate-positive solution for a circular economy.
Škoda Elroq
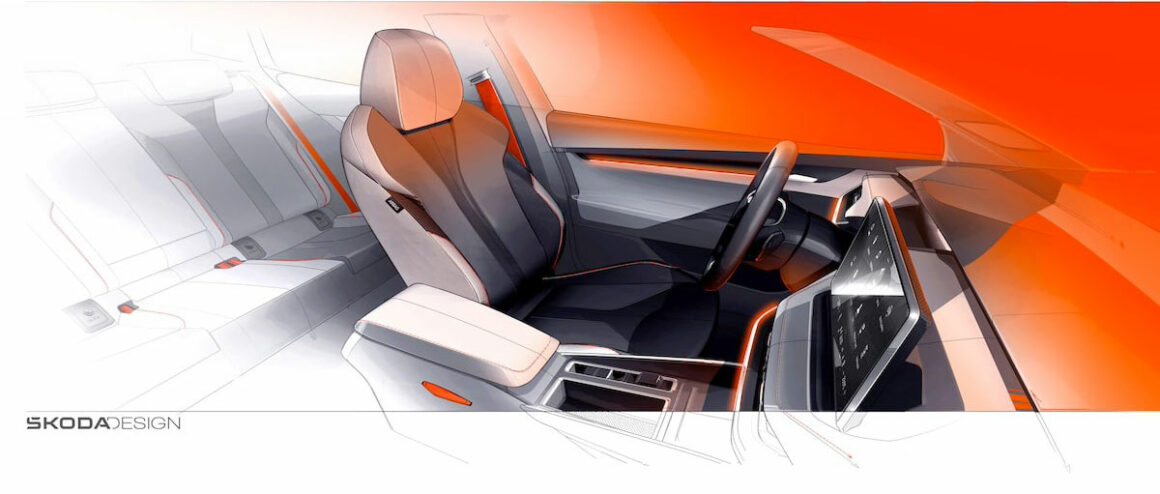
The new Škoda Elroq uses advanced sustainable interior materials, including Recytitan and Technofil. The seats and upholstery fabrics are made from recycled plastic bottles and, for the first time, recycled clothing. These are carefully reprocessed into high-quality new yarns and fabrics for the Elroq.
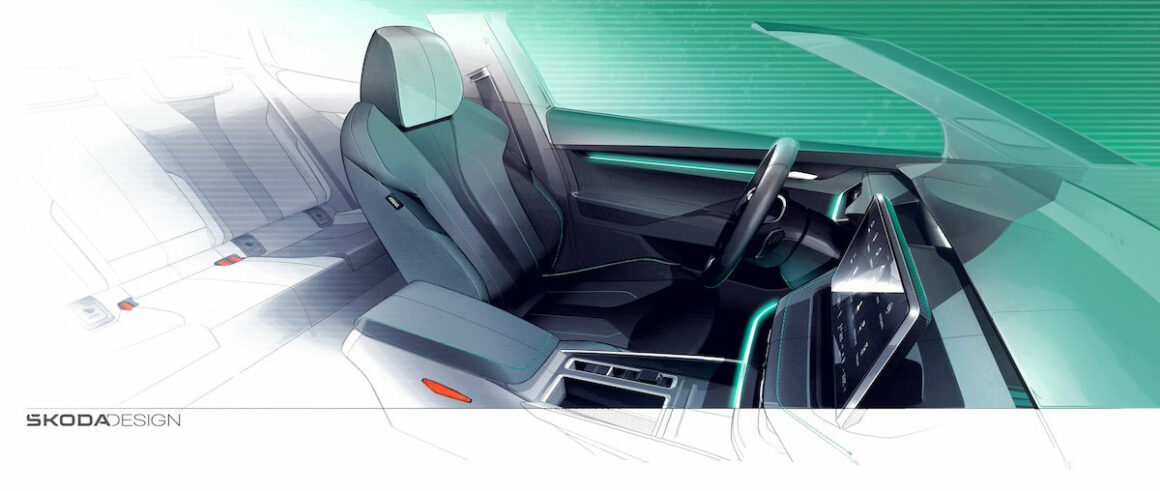
Recytitan is used for the door panels, seat covers, dashboard, armrest, and knee pads. It is made of 78 per cent recycled PET from the likes of plastic water bottles. In the Lodge Design Selection, Škoda uses Technofil, which contains Econyl yarns made from reclaimed nylon from old fishing nets and fabric scraps. Lodge pairs black fabric with light grey artificial leather, highlighted by orange contrast stitching and matching orange seat belts.
Careful attention to detail during the spinning and warping of yarns ensures a perfect balance of comfort, durability, and sustainability. The remaining material is derived from new PET (16 per cent) and, for the first time, also mechanically-recycled fibers recovered from post-consumer clothing (6 per cent).
Kia
Kia has been developing a broad range of natural materials.
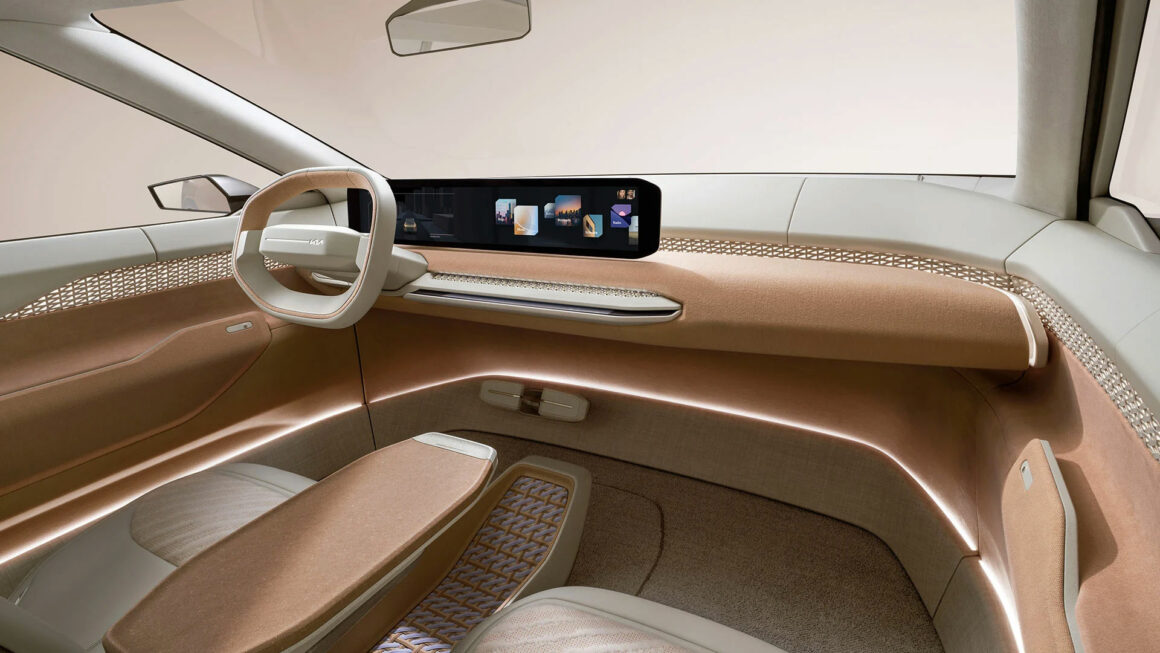
Their CMF design team took inspiration cues from Earth to create the EV4 concept’s cabin. By applying natural dyes to recycled cotton, using madder roots and walnut shells, the team can provide a wide range of colors.
Already, Kia says they have successfully implemented more than 30 sustainable solutions in various product areas, including fabrics and carpets using recycled PET, bio-based alternative leather, and paint free of benzene, toluene, and xylene (BTX). Additionally, they say 20 per cent of all their vehicles’ plastic parts will be made from recycled plastics by 2030.
The company also has committed to completely phasing out animal leather in all future products. Instead, they’ll replace both leather and PVC with bio-polyurethane derived from the likes of corn and eucalyptus. They say this material is an optimal leather replacement, since it incorporates plant-based components and provides excellent support, cushioning, and durability. Kia says this move will reduce CO2 emissions and the use of toxic chemicals, without sacrificing durable design aesthetics.
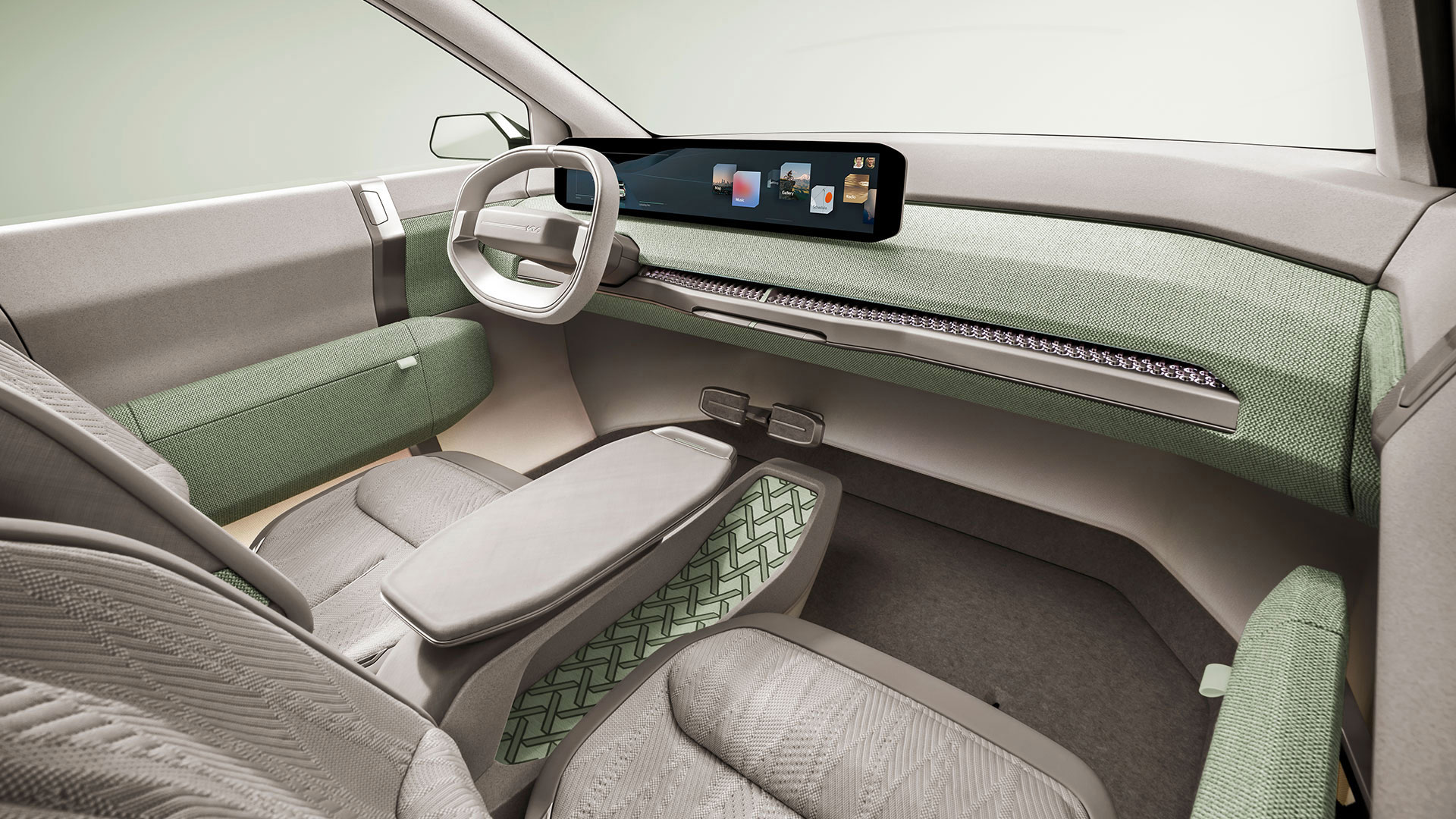
Kia wove fabric stripes by hand and applied them to create a 3D knit finish effect to the concept car’s seat covers.
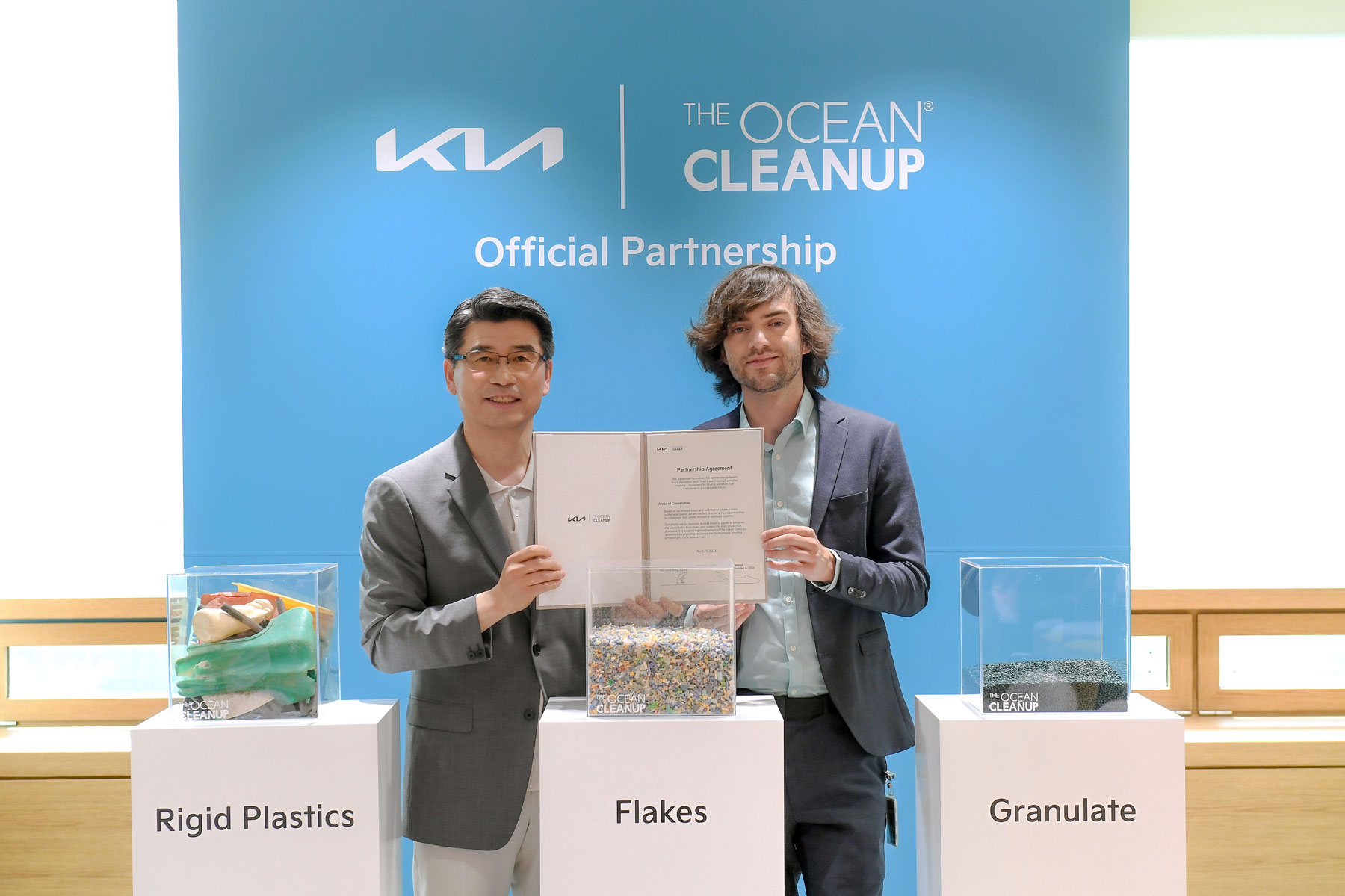
Kia also plans to focus on what they call ‘bio fabrication’, and to this end, they have partnered with South Korean startup Mycel, which produces fungus-inspired biomaterials. Fungi are well known for decomposing organic matter. The branching threads of fungal mycelia, called hyphæ, can break down long chains of hydrocarbons, including some plastics and unrefined oils.
Seoul-based Mycel has focused on the role of fungi as a link between industrial systems and natural ecosystems. Kia says Mycel’s technology could un-doom billions of livestock animals and reduce greenhouse gas emissions.
Kia’s Head of CMF Design Marília Biill says, “Using Mycelium enables us to mimic the processes we see in nature and leverage it to design more sustainable solutions. The material can be grown in any shape you want using a mold. The use of Mycelium is still at a very early stage, and, as part of Kia’s sustainability strategy, we are working with partners to accelerate development of the material. One day, by growing our own materials, we’ll be able to simplify processes, adapt forms, and—most importantly—be closer to nature in its essence”.
Circularity and the Automotive Industry
Automakers and suppliers are working to improve sustainability in the automotive industry, in part by accelerating the circular economy. Unlike the prevalent linear economic model, wherein products are made, used, and discarded, in the circular-economy model products are designed and built to remain in use for as long as practicable. Then materials are recovered and reused to the extent practicable at the end of life, reducing the need for virgin materials and helping keep materials out of landfills and our environment.
To achieve circularity, automakers and their suppliers—nudged along by regulations such as the E.U.’s ELV (End of Life Vehicles) rules—are rethinking the entire vehicle life cycle, from design to manufacturing and maintenance to end-of-life. Realizing a circular economy for vehicles will reduce their environmental footprint and help keep plastics and other materials in use and out of our environment.
As automakers commit themselves to circularity, chemical suppliers who provide plastic- and polymer -based parts are increasing their use of recycled materials. This reduces demand for virgin materials, and helps reduce CO2 emissions over the lifespan of the vehicle.