By Paul-Henri Matha, DVN CEO
I went to Gothenburg in August, when southern Europe is enjoying holidays, but northern Europe is already working again. While there, I spent time with Polestar’s lighting design team to discuss their latest products.
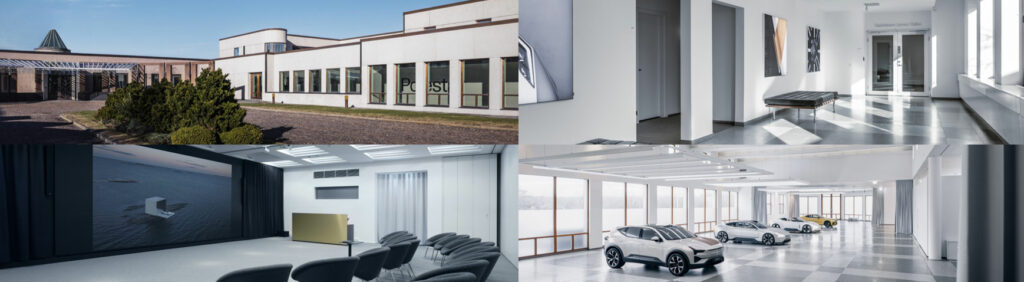
Exterior Component Design Manager Christophe Ferreira is supported by Lighting Studio Engineer Andrea Camuso, who started his lighting career at Valeo Italy; he was Valeo’s resident engineer at Ferrari.
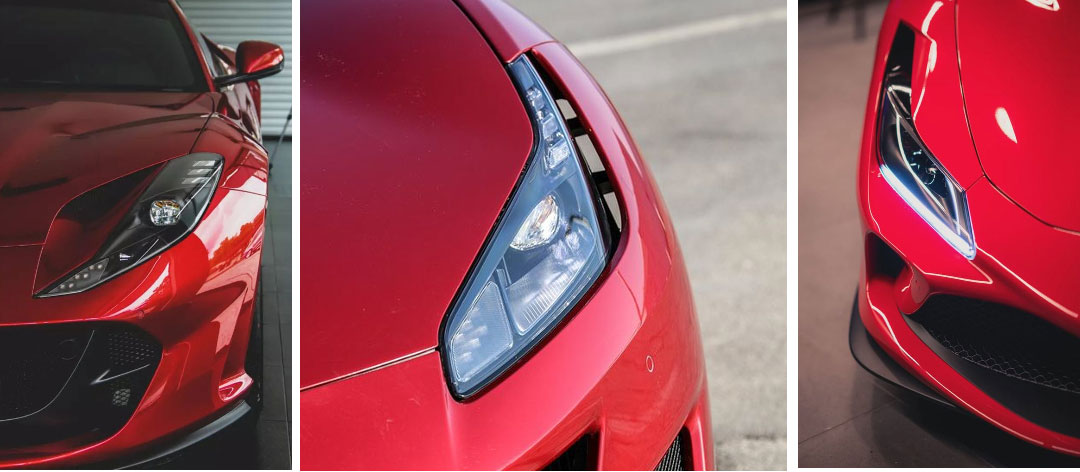
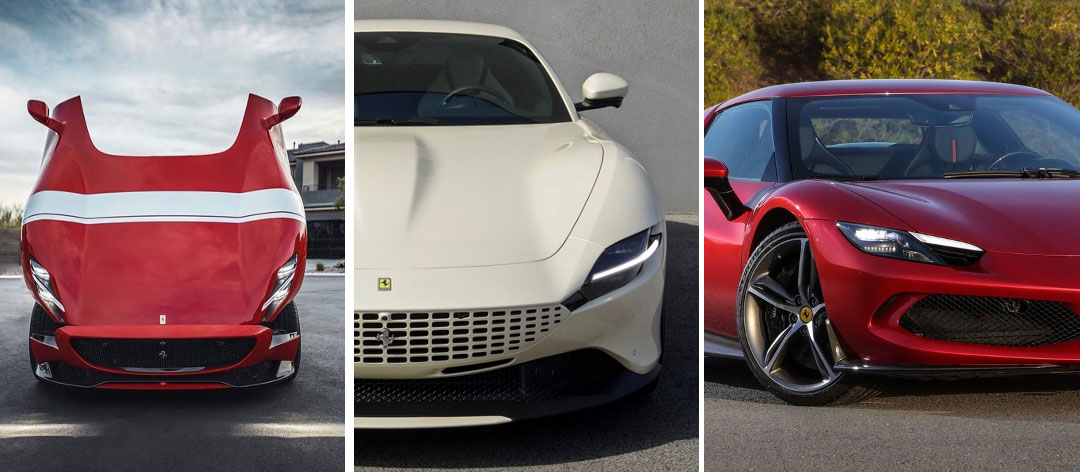
Then he moved to Lamborghini’s lighting development team.
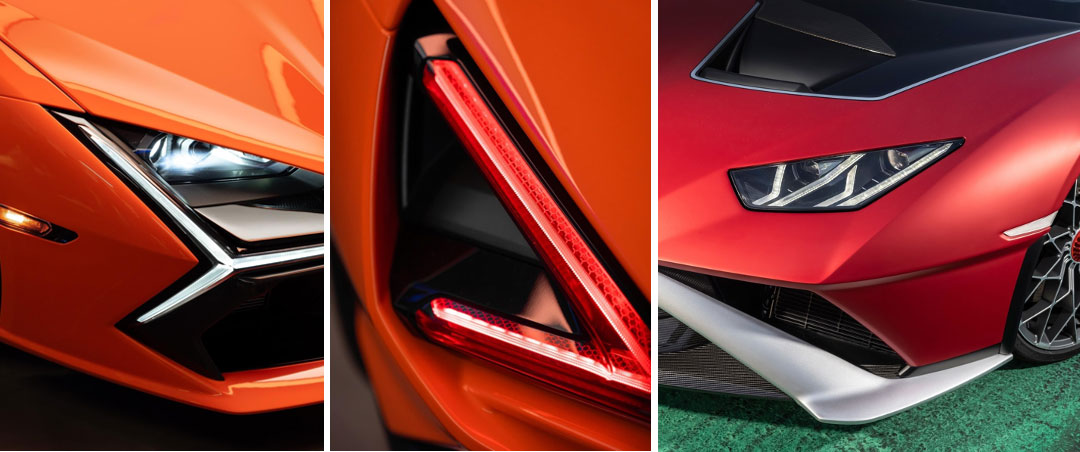
Sports car design is surely a specialty, with lamps embedded in the hood, and rear combination lamps right next to a V12 engine in a 250°C environment.
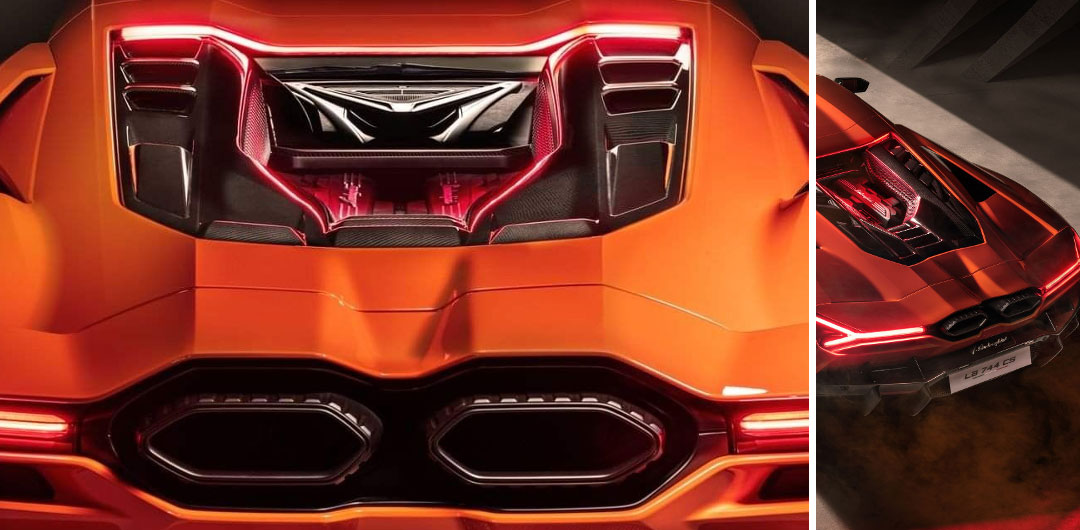
Perhaps because Italy’s weather was too good for him, he decided to move to Sweden in 2022 to develop Polestar’s lighting design philosophy.
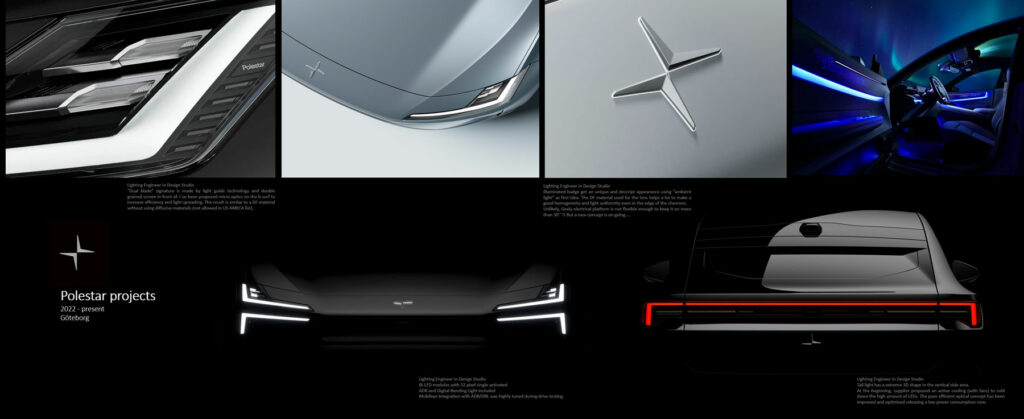
The latest Polestar models on the road are the 3 and 4. The Polestar 4 has an interesting front logo with a lit contour—really a beautiful effect!
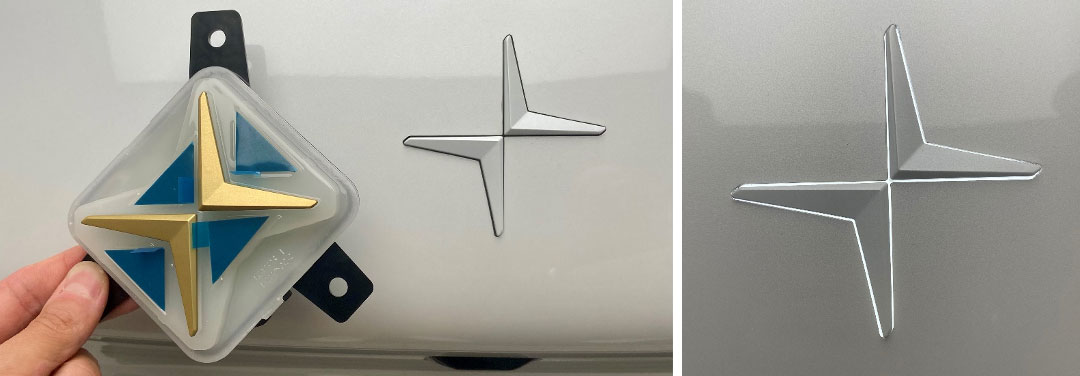
The next models to be launched will be the 5 and then the 6, based on the BST concept shown in July 2024. Christophe Ferreira and Andrea Camuso shared their thoughts with me:
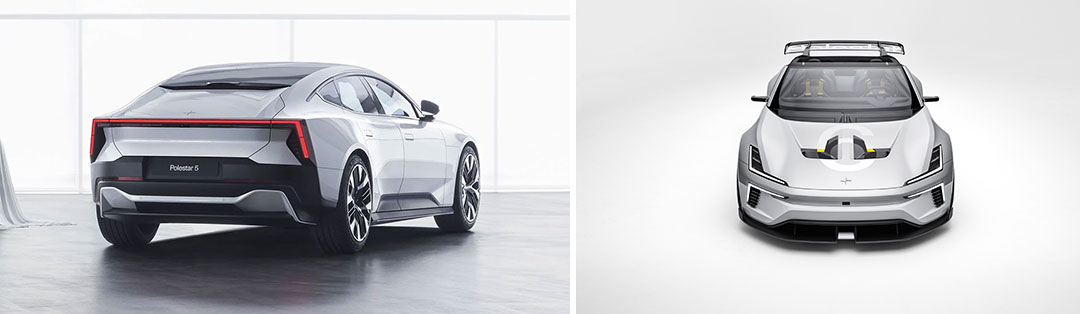
DVN: Can you describe your daily activities?
Christophe Ferreira: Since we are working on advance and production, our day can be varied and some days on a high pace rhythm; the tricky part for me in this case is to quickly switch from creative work to a more rooted, production-oriented topic, and then switch back to creativity, but that’s exciting with my role also. I am never bored.
Andrea Camuso: My daily work is fascinating. Engineers and designers don’t have the same approach on things, and I am the link between them, it’s extremely fun and challenging for me. Working side-by-side with Christophe and the designers is rewarding and productive to get good quality on the final parts on the vehicle. I’m providing them the technical support they need for the pre-feasibility phase, and keeping an eye on legislative constraints and new future possibilities. Another big part of our job is the perceived quality of the lamps—an important mission for us, to maintain our standards at the highest level.
DVN: Polestar’s design centre is not close to the R&D team, as it is in other automakers, and there are different platforms involved; how does the teamwork…work?
C.F.: Our R&D team is linked to the platform we are using. If it’s a Volvo platform, then it’s Volvo R&D, or same with Geely. Our R&D core team is in the UK and supports us on our in-house platform like the Polestar 5, and also on advance work. They are experienced engineers with expertise in premium brands, and we are happy to have Nick holland, Benjamin Aubert, and Harry McVicar with us.
DVN: Is it difficult to work with the Polestar R&D team in Coventry, England, on the other side of the North Sea?
A.C.: I would say the workflow is pretty fluid despite the distance. We do a lot of online meetings. The UK team is doing great and supporting us for our lighting strategy and taking care about the Polestar 5 and 6. Their expertise ensures all the interfaces between the lamps and the electronic platform, taking care about the development and the management of the lamps, and keeping the project on track.
DVN: Andrea, you are a lighting studio engineer, which is not a very common position. Some automakers have just a design studio with designers, and R&D with engineers. At Polestar, you have this engineer in the design studio. Tell about that, will you?
A.C.: As you know from your deep experience, exterior lighting is a really complicated and complete field. It’s the only component in the vehicle where we develop exterior and interior design. This small illuminated device combines four big fields: mechanics, optics, electronics, and legislation. Due to this complexity, it’s fundamental to have a proper pre-development phase, where designers are guided properly during the concept phase. Fighting with the legislation is always tough to understand, and Polestar designers are pushing the boundaries to deliver the best designs. It’s crucial for them to know from the beginning of the project where the functions must be placed, and adapt their concept accordingly. We are a design-driven company, and the competition is strong, so having studio engineers walking among the designers is fundamental to keep our leadership in design.
DVN: Christophe, what do you think of this approach? if I am correct, it was different at Renault where you were before.
C.F.: Yes, having an in-house studio engineer is mandatory for me to deliver realistic concepts. For Renault, the borders started to move in the lighting department—Sebastien Leone was with us three days a week, bringing his R&D expertise to design, and I would consider his role at that time like a studio engineer.
DVN: What will come next; what’s in your pipeline? What lighting technologies have your attention?
C.F. & A.C.: We are in constant search of innovation, scouting the latest tech that will help us deliver the best designs, and continue to provide innovative solution focusing on compact packaging and top-notch homogeneity; for example, the Polestar 5 rear lamp.
Sustainability and performance are also big pillars in our design. One of our main deliveries will be what we call the Polestar 0 Project, to create a truly climate-neutral car by 2030. Becoming climate-neutral means eliminating all greenhouse gas emissions across our operations and all phases of our cars’ life cycles—lamps included! We try to get designers familiar with our main three pillars for a sustainable lamp: keep it light (weight reduction), keep it efficient (power energy reduction), keep it simple (small size, few components, recycled materials). At Polestar, our approach is design following the function, so it leads us naturally to sustainable concepts.
DVN: Considering that in this interview you’re addressing the whole vehicle lighting community, what do you think is missing? What do you need or want that doesn’t presently exist or could be improved?
C.F. & A.C.: Polestar is well known for our sustainable approach. What we miss today is innovation into new materials. I remember Ford’s 2019 experiment with coffee bean waste to create a lamp housing, so my question would be: where are we today?, How can sustainable materials like Bcomp or Papershell be made compatible with our exterior lighting requirements?