Have you driven a car designed, developed, or engineered by Italdesign? Probably so! Since creating the iconic Alfa Romeo Alfasud in 1971, Italdesign has created models for the world’s automakers—over 60 million Italdesigned cars on the road worldwide. Vertically integrated from design to engineering, testing, and validation, Italdesign remains a trailblazer in the automotive world.
Founder Giorgetto Giugiaro, together with Aldo Mantovani, are giants in the Italian design industry. They and their associates and successors have propelled Italian car styling to grand heights. We talked and listened with Italdesign’s CTO Davide Casini; Concept Development & Virtual Validation Team Leader Matilde Piccione, and Gian Marco Tassi, an Italdesign Passive Safety Development specialist:
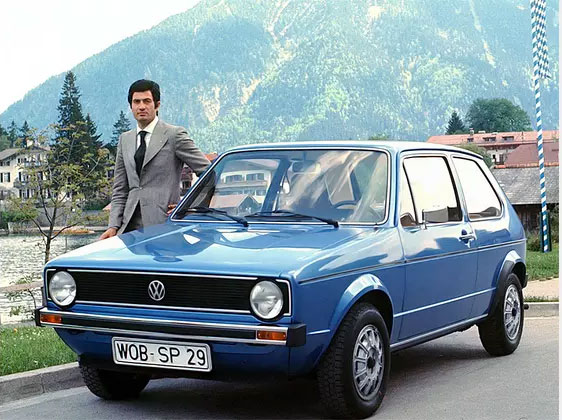
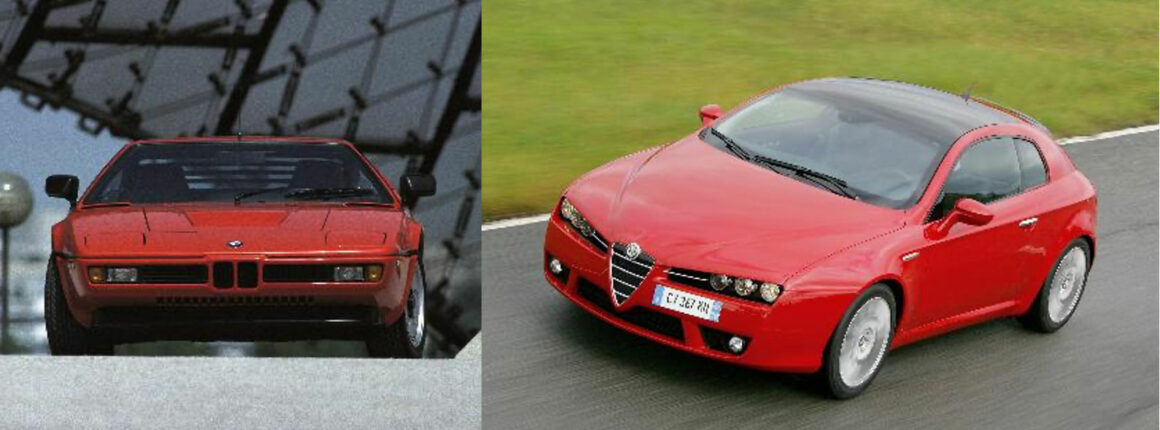
DVN Interior – Olimpia Migliore: Tell me about Italdesign’s capabilities.
Davide Casini (CTO): Italdesign can provide vehicle development services from styling, therefore design in the strict sense of the term, to engineering, pre-production, or production of small series.
Design starts from the initial conceptual sketches, continues with the analysis of the user experience, the creation of all the internal and external surfaces, and all the style convergence activities done in cooperation with the engineers. The design that is developed, in addition to responding to customer needs, also responds to legislative and manufacturability needs, so it is never just styling, but design ready to be engineered and manufactured.
In the engineering field, our company is able to start from the concept and get to the production start. The services cover the development of the body, of the components and systems, including the virtual and physical validation.
We are also able to coordinate and steer the tier-1s, and also after supplier nomination we can take care of the completion of the project and production.
DVN: How do you handle electronics?
D.C.: in the electric-electronics field we essentially deal with the application of available systems of ADAS, HMI, connectivity platforms and e-traction, with part of the software development done internally, such as high-level HMI graphic interface softwares.
The lower-level ADAS or connectivity software normally comes from the OEM as a ready-to-use platform, while we provide the application and adaptation to the product we are developing.
DVN: How about prototyping and validation?
D.C.: In the pre-industrialization and industrialization phase we can produce all the necessary prototypes internally, but those are increasingly less requested for reasons of time and costs and because virtual development tools are very reliable today.
As an engineering team we are also able to do the entire validation phase of pre-series already built in the production plants or we can produce small series, from one to a hundred cars per year.
DVN Interior: Where do you build these prototypes and cars?
D.C.: Moncalieri, Vadò, and Nichelino, therefore within a radius of 10 km around the headquarters.
DVN Interior: Can you walk us through an example?
D.C.: The Nissan GTR 50, whose design comes from the OEM, while Italdesign has taken care of the entire engineering, validation and construction part (about 20 cars). In fact, we can define ourselves as a one-stop shop, from style, to setup, benchmarking, engineering, up to production startup. Except for process engineering of big volumes, of course, since this is strictly linked to the manufacturer’s plants and existing machinery. while in case of limited internal productions, such as the GTR 50, we were also takin care of with the process engineering, which obviously follows the logic of limited productions and not large series.
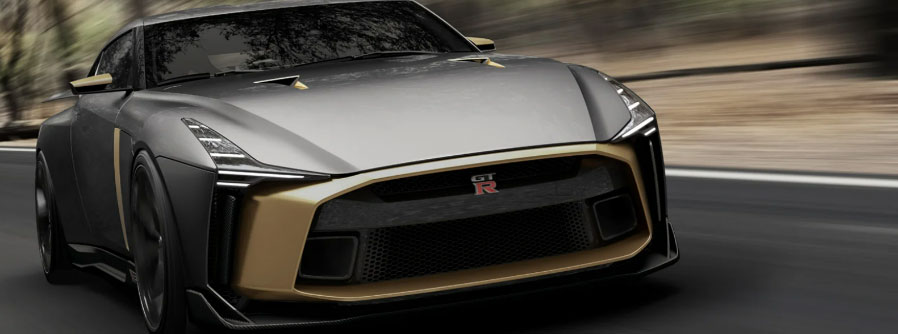
DVN: Are the skills for all these activities exclusively internal?
D.C.: Almost. We also rely on external partners and suppliers, but only to expand our skills and knowledge. For example, if we receive instructions for the installation of a component from our customer, we first try to understand how it works and how it can be best integrated and, if necessary, we also indicate to the supplier the changes necessary to adapt it to the vehicle we are developing. In essence, we always look at the project as a whole, not at the individual component or perimeter. When the client submits a project to us, before accepting it we formulate a whole series of questions, which at first may seem excessive or redundant for the client, but whose value in the end is recognized as a proof of our competence and efficiency, because they anticipate problems that are perhaps not very evident at the beginning.
DVN: Would it be fair to say this part of your competence has developed in the last 20 years?
D.C.: this is a perception that is not completely correct, because the heart of the company has always been design together with engineering, which, talking about the founders, was represented by Giorgetto Giugiaro and Aldo Mantovani. Giugiaro was a character, a name, he knew how to generate emotions. Design is emotional and therefore remains longer in people’s memory. Engineering is much more difficult to describe and make attractive to the general public.
DVN: What percentage of your turnover does it represent?
D.C.: Even if we are known as a company that creates style, engineering is in fact the heart of Italdesign from the beginning, it is the main business of the company and represents 80 per cent of the turnover. Today the engineering team has 800 people globally. 700 of whom are in Moncalieri. In fact we are a small OEM, being a branch of Audi and their technical direction and working 60 per cent of the time for them.
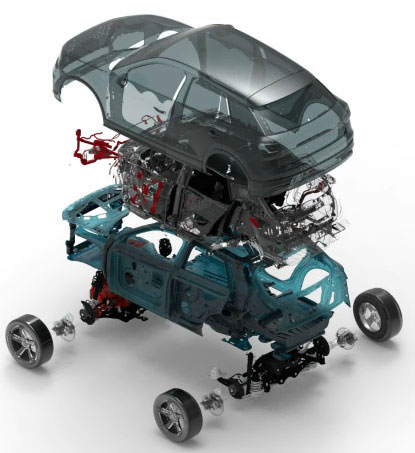
DVN: Your Concept Lab exemplifies Italdesign expertise and ingenuity, which is also particularly interesting for our readers because it is a tool for the development and optimization of car interiors. What can you tell us about it?
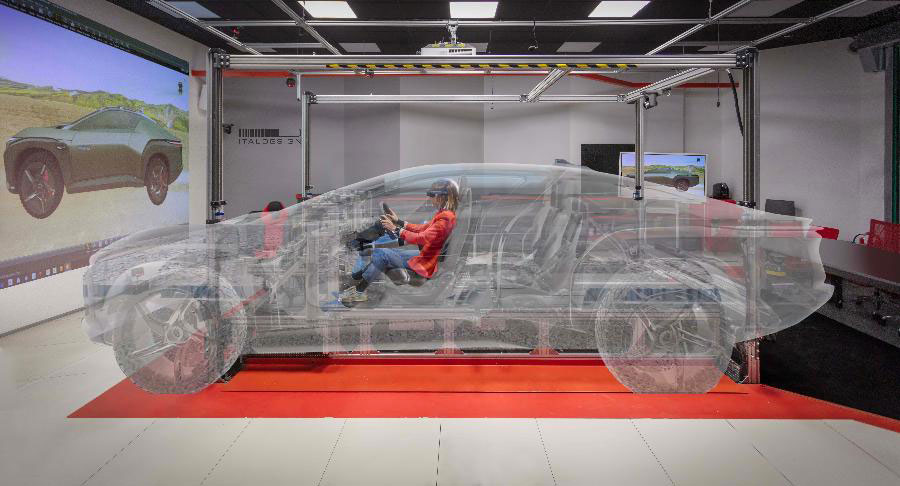
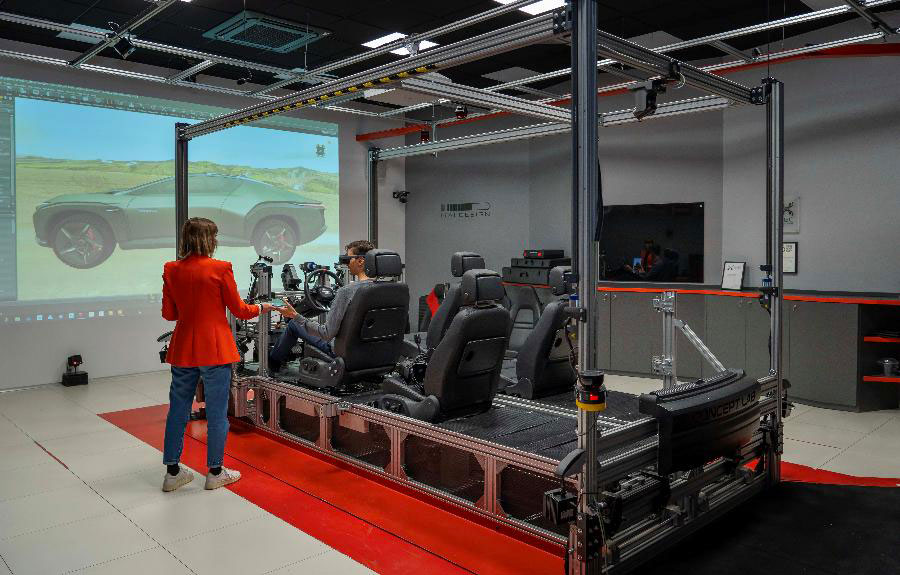
Italdesign, Matilde Piccioni (Concept Development & Virtual Validation Team Leader): The concept lab was born about eight years ago from an idea of digitalization of processes in the automotive development field and more generally in the transport sector. The goal was to digitize and optimize the product development process to overcome the constraints related to the creation of physical models for ergonomic validation and issues related to development times and costs.
We start from the very early stages of the project, with raw data, stages in which there are not even the mathematics or data to create a physical model.
With a tool such the Concept Lab it is possible, both from the point of view of the physical and virtual model, to set up a very first layout of the car and proceed in defining what is the macro setting and the hard points of the vehicle.
After that, throughout the development of the project, as the project phases progress and mature, it is possible to create more detailed sessions and therefore represent even more realistic and more substantial layouts in terms of details, both from the point of view of the physical and virtual structure.
DVN: How are the physical systems made?
M.P.: The tool consists of a physical mockup and is composed of a load-bearing structure that replicates the floor of the vehicle, with the seats, doors, pedalboard and steering wheel. All the elements are adjustable in various directions, so everything can be positioned to represent different layouts of the car, from sports cars to commercial vehicles. Everything else is then integrated with virtual reality technologies.
One of the main advantages compared to physical models is the optimization in terms of physical parts, therefore of material, not only linked to the development time, but also a saving in terms of materials, therefore energy efficiency and raw material.
DVN: Do you have a database that can be integrated in the virtual reality software to reproduce the textures or the type of material?
M.P.: With the support of virtual technologies the materials are rendered, therefore the various materials are visually represented, but the possibility of having tactile feedback of the materials is not yet implemented. But the technology development is supporting us more and more in that direction.
The trend is to increasingly minimize physical elements and realize only part of them, possibly with more sustainable technologies than in the past. So, if in the past the direction was to mill elements of a certain size inside the hardware, today there is a greater tendency to work with small partials made in 3D printing and with more sustainable materials if needed.
DVN: What was the Concept Lab originally meant for?
M.P.: The Concept Lab was born mainly for ergonomic validation activities, therefore everything that is the performance of reachability, visibility, reflections, habitability, a mixed approach between physical and virtual reality.
In the field of software development, we have managed to integrate, within the same setup, activities more related to the style and benchmark of competitor vehicles, therefore the comparison between different models, different style layouts or more technical layouts. All this with a simple switch, always sitting in the same car configuration or changing the layout, all in real time.
DVN: So everything, the hardware and software, is in-house by Italdesign?
M.P.: Yes, the software was developed and patented by Italdesign and the methodology and the application behind this combination of hardware and software parts are patented. The user experience that we can recreate with this setup is also proprietary to Italdesign.
One of the technologies that we use in the virtual world is a tracking system, on the shelf, that we have integrated with the rest of the equipment and customized for our specific use cases.
This allows us to track the elements of the physical world, whether they are elements specific to the car such as the seat and steering wheel, or the body parts, so the hands or the entire body of the user. With a perfect alignment between the physical and virtual worlds.
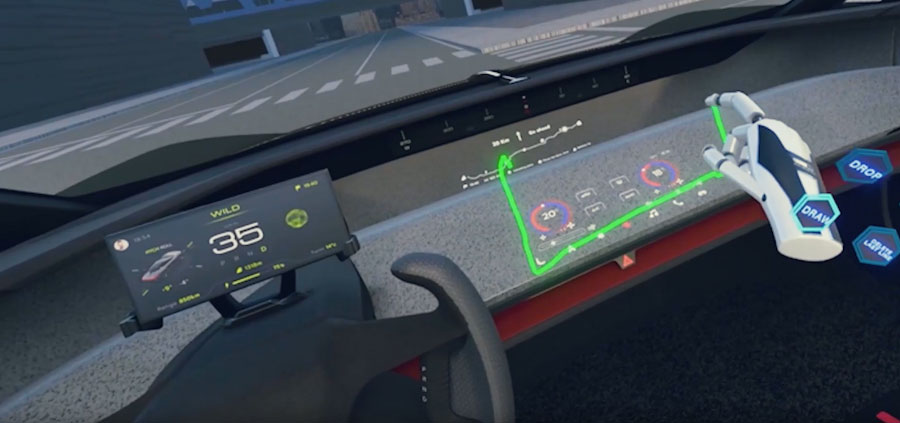
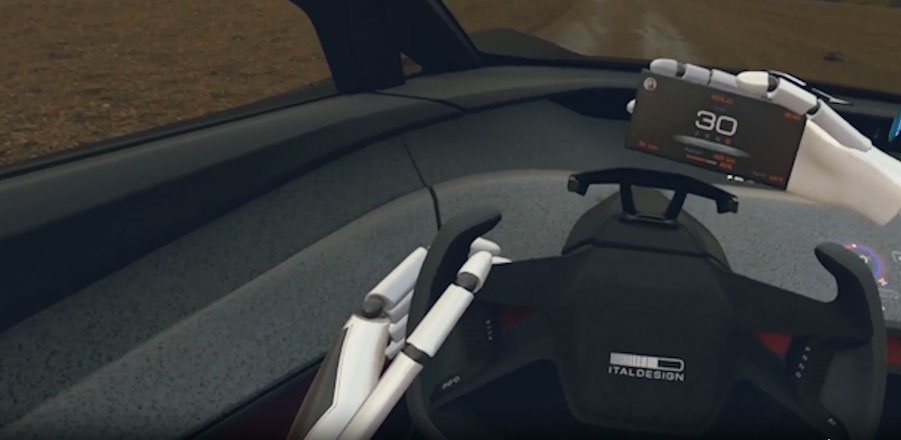
DVN: Taking seat development, for instance, historically seats have been developed only for the standard percentile, and not the 5th and the 95th. With this tool you can design for everyone?
M.P.: Yes, for example, in the case of seats, it is possible to simulate from the fifth percentile up to the 95th, allowing to collect a series of subjective data and objectify them in addition to the predictions that are made in the design phase with conventional CAD tools for standard percentiles.
The data is then validated with clinical tests, with adequately selected population samples that are involved and then interviewed to collect subjective feedback, not exclusively linked to body size and therefore to the percentile, but also to comfort and ergonomics.
DVN: Do you benchmark competing models?
M.P.: Yes, the possible combinations are infinite, in the sense that by combining and minimizing the hardware parts and customizing them, working on the virtual environment, it is possible to recreate different setups, different scenarios and different sessions depending on the project phase and the purpose of the session.
The tool is also made for that, so to define the hard points of the car in the preliminary phases of the project, define the seating setup, so the position of the seat and steering wheel, and also support us in those activities of convergence with the style, that is to say everything that is the meeting point between the styling creativity and the translation into engineering technique.
DVN: In the early stages of a project, is your interaction mainly with the OEM style centre?
M.P.: In reality, car development has changed a lot in recent years. The user is always at the center of development so whoever designs the car interior is strongly guided by consumer research and design studio. But the interaction with engineering is very strong right from the start because the technological contents are increasingly higher.
The Concept Lab is very useful for the development of the HMI of a touch screen, for which the evaluation of ergonomics and user friendliness is done in a completely virtual environment, with development times and costs that are dramatically reduced.
The situation in which the simulation environment is made dynamic, finally allows to simulate infinite combinations, by adding a driving experience on the road, with factors such as digital distraction which can be evaluated. The dynamic context is certainly more faithful to a real experience.
DVN: What other car interior situations can be simulated?
M.P.: Lightingcan also be simulated, and there are also tools to check the reflection of the screens in various light conditions, or how the screens are reflected on the external mirror.
Or you can use the Collision Tool, a tool that allows us to perceive a response, a feedback in terms of vibration, sound and color when you intercept the virtual surface.
In this case, gloves are worn, part of the tracking system. For these gloves, a software has been developed that allows us to perceive something upon contact with a virtual object. For example, for a display installed in the centre of the car, I can evaluate when I can actually reach the display or, if the display is too far away, evaluate what is the distance between my reachability area and the virtual component.
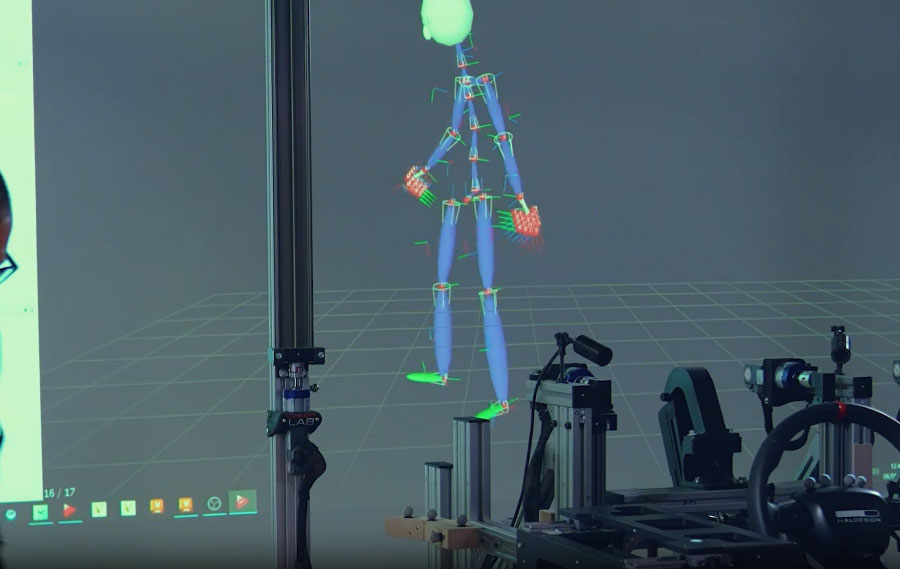
DVN: And you can also connect this to the seat position.
M.P.: Yes, absolutely, when users gets on board they can adjust the seat and the steering wheel position exactly like in a car. At that point it is also possible to do reverse engineering, so freeze the positions chosen by each individual user and go map each user during the clinic test. Later, after the clinic, it is possible to redraw some points to see the various selected percentiles and see how they are placed within the preliminary layout that we are studying.
DVN: What about with autonomous driving, when the seats might be in unusual positions?
M.P.: You can adapt the position, by turning the seats or changing the seats, from those of super sports cars to trucks. For trucks for example, a possible analysis is the one of the blind spots, that is, if I can see the pedestrians around me. We were able to compare different models simulating the passage of pedestrians in different positions and the user was able to actually see, with the different style and engineering solutions, what was the driver perception, and the vision around the vehicle.
DVN: So you can simulate the interiors of VTOLs or the future mobility before it is even built?
M.P.: Absolutely, yes!
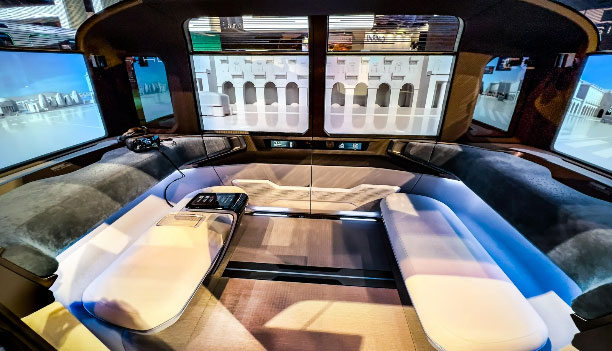
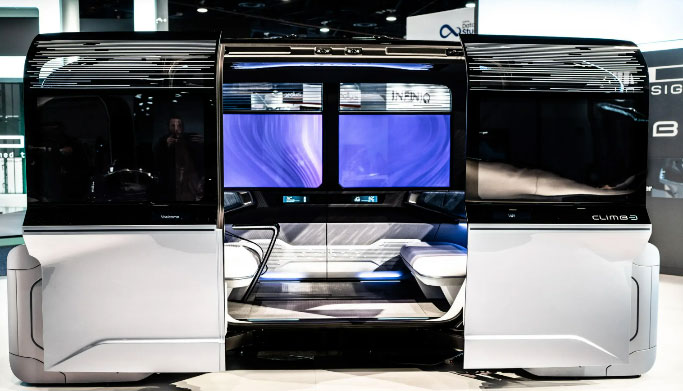
DVN: What are the development times like?
M.P.: a complete exterior-interior physical model requires a development of about eight weeks, so two months, between the design phase and the mathematics and the assembly and realization of the physical object. A session in Concept Lab can last from a few days to 3-4 days to a couple of weeks.
For the setup of a complete experience, with clinic tests and final presentation, development times are reduced by over 50 per cent, and consequently also the costs related to the creation of the different scenarios.
So less time, but lots of content.
DVN:Let’s talk about innovation. What process do you follow for innovation? What are your sources of inspiration?
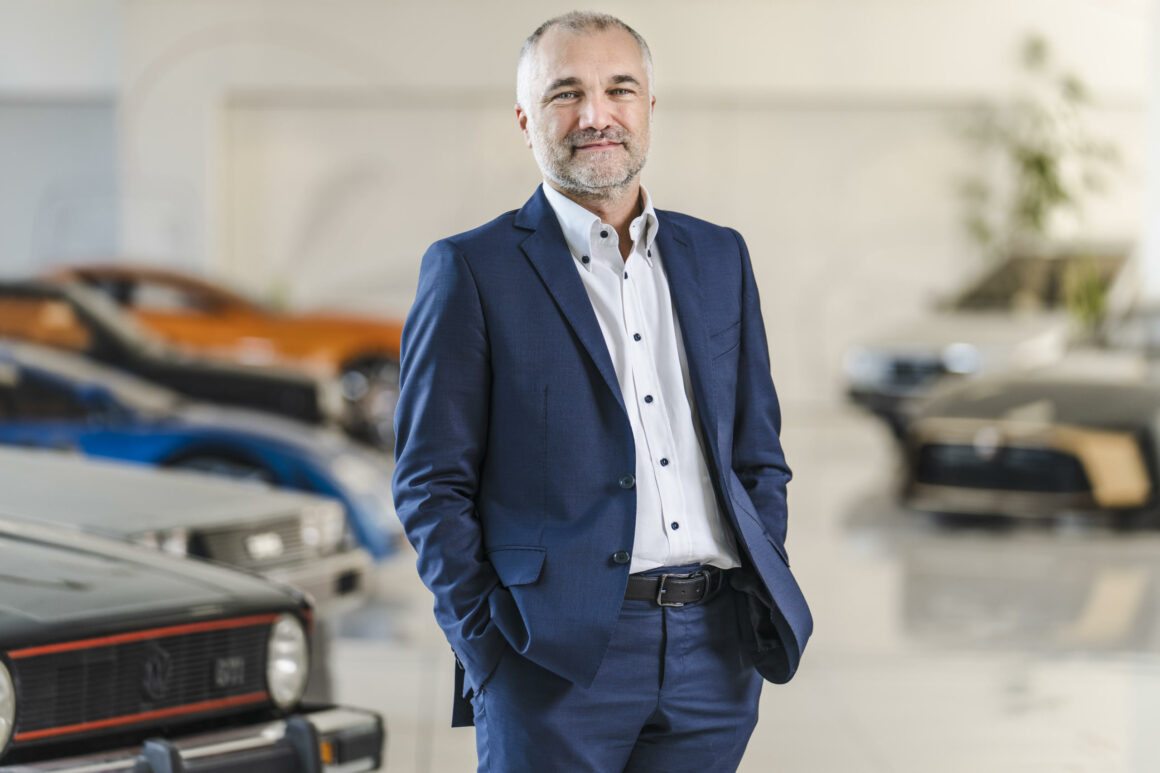
D.C.: Innovation at Italdesign can arise from requests from customers who come to us with a certain type of problem and ask us how to solve it in a different way than how it is normally faced.
Or—and this is a large part of the innovation we do—it is born within our company. Since we ourselves are users of our product, we analyze the problems and our desires, things we would like to be different in our car. All Italdesign employees are free to propose ideas.
DVN: How does that work?
D.C.: Typically, colleagues propose the idea to their area manager as a first step and then the ideas are examined by the two innovation project managers, Elena Negro and Nikolas Vinci. They collect the ideas and begin a process of evaluation and validation of these ideas, evaluation and validation.
We go and do market analyses, and if necessary internal or external surveys, to understand if we are going to hit a problem that actually needs a resolution.
We then typically develop a proof of concept and a business case analysis.
DVN: What type of data do you use to validate the idea?
D.C.: We have data on the costs of hardware and software in the automotive industry, so we are going to estimate the cost of our object compared to those that are standard content.
In the example of an innovation that we recently developed, a new type of airbag, we know the development costs of an airbag well but also the construction costs. In that case we combined the cost of the belt and the airbag bag to the best of our knowledge to estimate what the cost of the final product would have been.
DVN: So, innovative products and processes. Do you have some favorite examples?
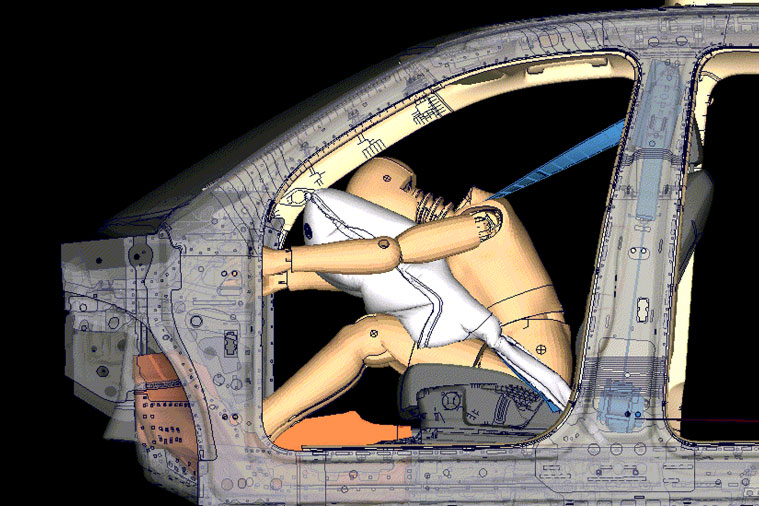
Italdesign, Gian Marco Tassi – Passive Safety Development:We developed a new type of airbag integrated into the seat belt. We started from the following problem: let’s imagine in a self-driving car that we no longer have a traditional dashboard: if I don’t have a place to install an airbag anymore, where am I going to place it?
Among the various alternatives, we said, why don’t we go and put it on the abdominal branch of the belt? So we built a dummy, which was mounted on a super sports car and an SUV.
We did static and dynamic clinic tests. Potential customers first put the belt on statically, to get the feeling of what it would be like in the car. Then we gave a test matrix to the user by telling them to put it on, take the belt off, then put it back on, then start doing some types of movements and describe the feeling you have. We did the test with and without, to compare on two very different types of cars.
DVN: Were there dynamic tests, with cars on the road?
G.M.T.: We also went on the road, to see what the customer felt like. We then went to do the validation in the event of a crash, so we could be sure that the performance that is given is similar to that of the traditional belt plus airbag system.
We also took pressure measurements on the abdomen, to be sure that we were not going to generate damage to the abdomen during airbag deployment, and simulated misuse tests and extreme cases, so 5th – 95th percentiles, or conditions in which I cover the bag with my jacket, conditions in which I stand crosswise, conditions in which instead of protecting the user there is the risk of causing harm, or if I travel with a tablet.
We then did a full cost analysis, that is, how much is the development cost of the bag and belt system and the bag on belt system, how much is the cost of the variable, how much is the cost of validating the system and in fact we came to the conclusion that a system like this gives economic benefit both in terms of development costs and in terms of the variable.
So, going back to the development process, it is a well-rounded process, that is, we analyze how the user would perceive innovation, what cost the innovation has for the OEM and for the user himself and the technical feasibility.
Furthermore, if before a car lifetime was 7-8 years, now it is only 3 or 4 and the next version must already have much more content, so we also need to anticipate times, offering innovative content to our customers, helping them keep up with technology development.
DVN: Fascinating! We could talk about your innovation for a long time but we will leave some surprises for our next Interiors conference in Cologne. Thank you very much to the whole engineering team, and we hope to see many of you in April in Cologne to illustrate your engineering services and new innovation concepts.