By Olimpia Migliore, DVN Interior Editor
Generative ‘AI’ is presented as a quick and powerful shortcut for easy solutions to complex problems. Today’s and tomorrow’s auto interiors are brimming with complex problems. Consider seats: safety, comfort, ergonomics, design, and ecocircular construction all have to be achieved at the same time, within tight cost and manufacturability constraints. Look anywhere else in the interior and you’re guaranteed to see more complex problems like this—the cockpit, the door panels, the roof system, the controls and displays. And then there’s the greater interior, which must be the kind of environment appropriate to the kind of vehicle: cozy and inviting, practical and functional, exciting and sporty. These conflicting simultaneous demands present great challenges and time-demands in designing components. Seemingly endless discussions are required between developers and designers to find the right compromises and balances among the many styling and engineering requirements.
So-called ‘generative design’ (GD) is probably not the pinnacle solution, but it surely can be a great help to achieve results in shorter times, and it can facilitate new kinds of creativity.
Unlike traditional design processes, wherein human designers create and refine ideas, GD uses algorithms to explore a vast number of design permutations based on predefined goals and constraints, such as ergonomics, materials, safety, and aesthetics. The idea is that ‘AI’ can evaluate a great many more permutations and combinations very fast, and from among all the permutations can emerge highly functional, personalized, and innovative car interiors.
The process can prioritize parameters like customer preferences and specifications, passenger characteristics, and many more. For instance, using data from human body scans, GD can develop ergonomic seating, ensuring maximum comfort and support based on driver and passenger profiles. It can customize the dashboard layout based on usability, accessibility, and safety factors. Generative algorithms can explore supernumerous seating configurations, dashboard arrangements, and storage placements, optimizing for space, comfort, and safety.
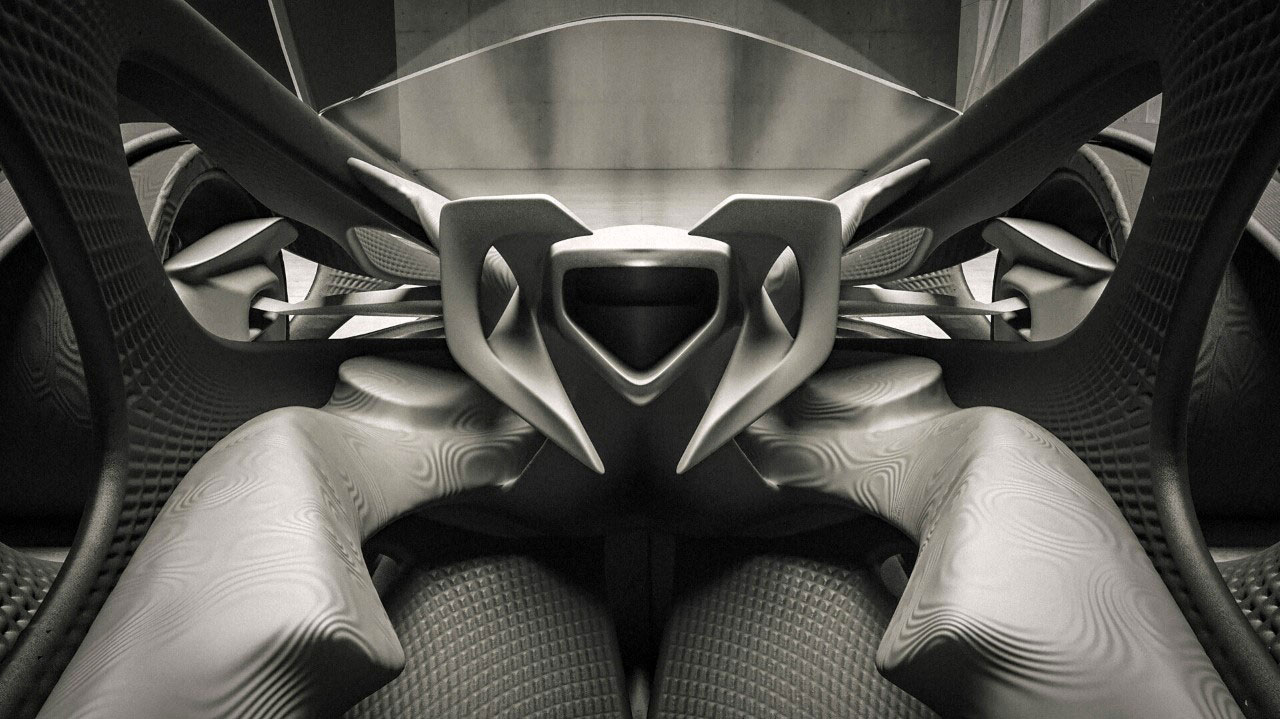
Additionally, generative design enables engineers to apply existing data to new platforms effortlessly to maximize the benefits of re-use, sparing design teams from spending time and resources redesigning vehicle systems that already exist.
GD can explore different material combinations—leather, fabric, sustainable materials—to create interiors that meet æsthetic and functional inputs while balancing performance, cost, and environmental compatibility. It can devise interior experiences, including mood lighting and surrounding music.
Generative design tools allow manufacturers to create virtual prototypes of car interiors quickly with 3D printing, which can greatly accelerate design iteration and testing.
It seems a GD business boom is in the offing; the global market size for generative ‘AI’ in design was estimated at several hundred million dollars in 2022, and it is expected to hit billions by 2032.
All this sounds great, so what’s the catch? This constellation of technologies and techniques is immature, and ‘AI’ still presents a lot of difficult, complex challenges like privacy and data security, ‘AI’ vs IP rights, and dependencies on 3rd-party platforms.
Especially alarming is the tendency of ‘AI’ to introduce and amplify bias and errors into whatever task it is given. When ‘trained’ on flawed, biased, and/or insufficient data—which, almost by definition, they are—the models amplify those flaws, biases, thand deficiencies exponentially. This is a serious constraint on the degree to which everyone involved can really replace human-centric processes with ‘AI’-centered ones.
There is high potential for the real, practical time and effort savings to be markedly less than the theoretical savings because the models must be driven and assessed, and unrealistic results discarded. That is because ‘artificial intelligence’ is a misnomer for the ‘AI’ that exists today, which is not at all intelligent. It is merely a high-speed prediction and pattern-matching machine, something like a turbocharged version of the autocorrect feature we all love to curse at on our smartphones—not capable of judging right versus wrong, only more-likely versus less-likely.
That will remain the case unless and until artificial general intelligence (AGI) exists. Microsoft cofounder Bill Gates said last year, « There is a robust debate going on in the computing industry about how to create it, and whether it can even be created at all ».
Nevertheless, there are some fine, successful applications of generative design in automotive interiors. Here are some of them:
Toyota
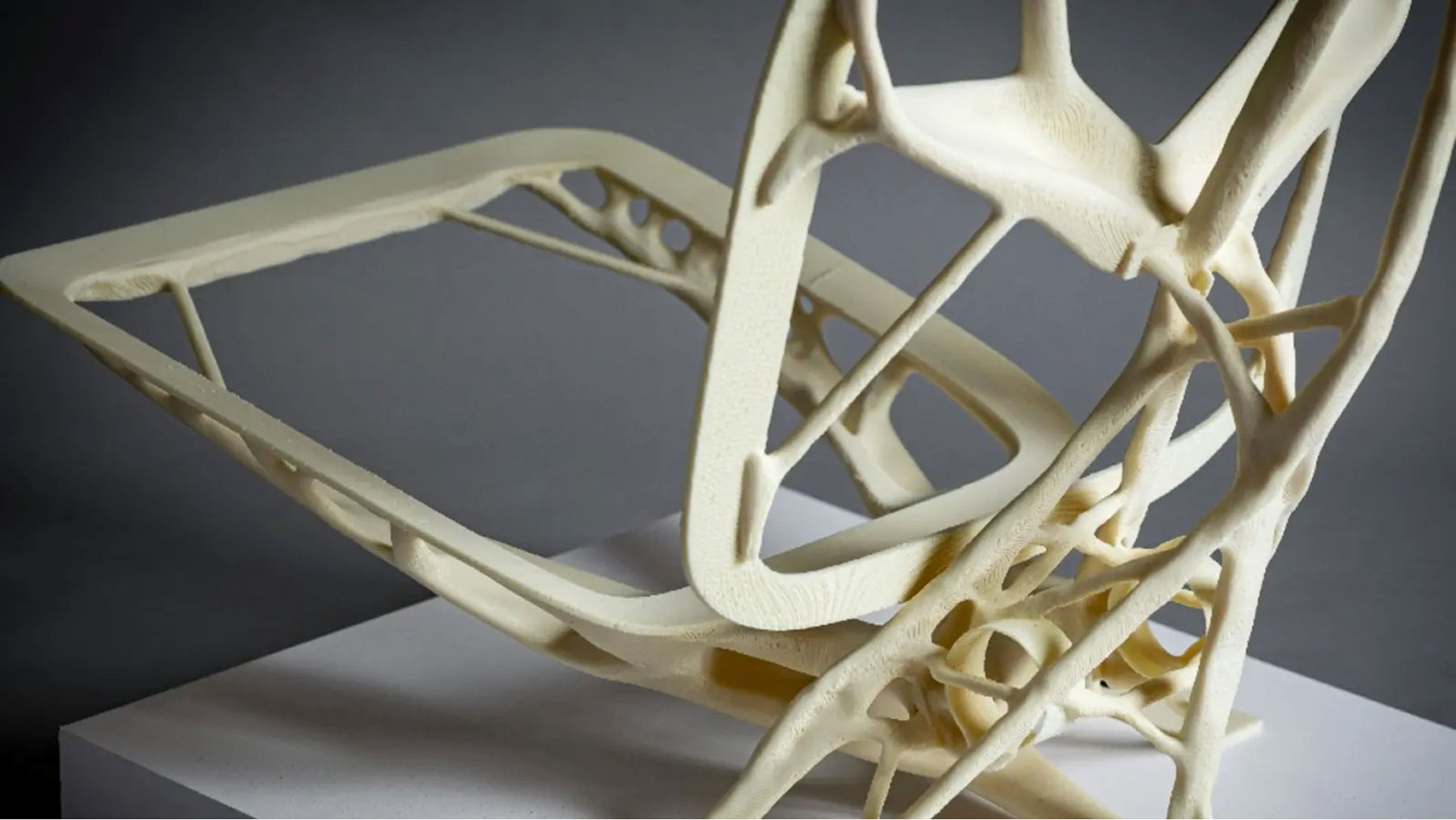
Toyota has been experimenting with an easier way to deal with all the variables related to seat structure development—safety, strength, weight, and thickness—to find the right balance.
Shinsuke Omori is a project manager in Toyota’s Vision Design Division’s Interior Design Department, and says, « while the current seat frame is designed to meet the strength requirement with trusted manufacturability, it is difficult to make it thinner (…) designers do not usually work on the seat frame itself, but rather add materials to it, and that’s the restriction ».
But Omori’s design team can explore shapes and features for seats without regard to the shape of current parts: « What we are focusing on right now is the balance between comfort, sustainability, weight reduction, and design », Omori says. His team is using ‘AI’ technology in the Autodesk Fusion 360 product, which is basically generative design.
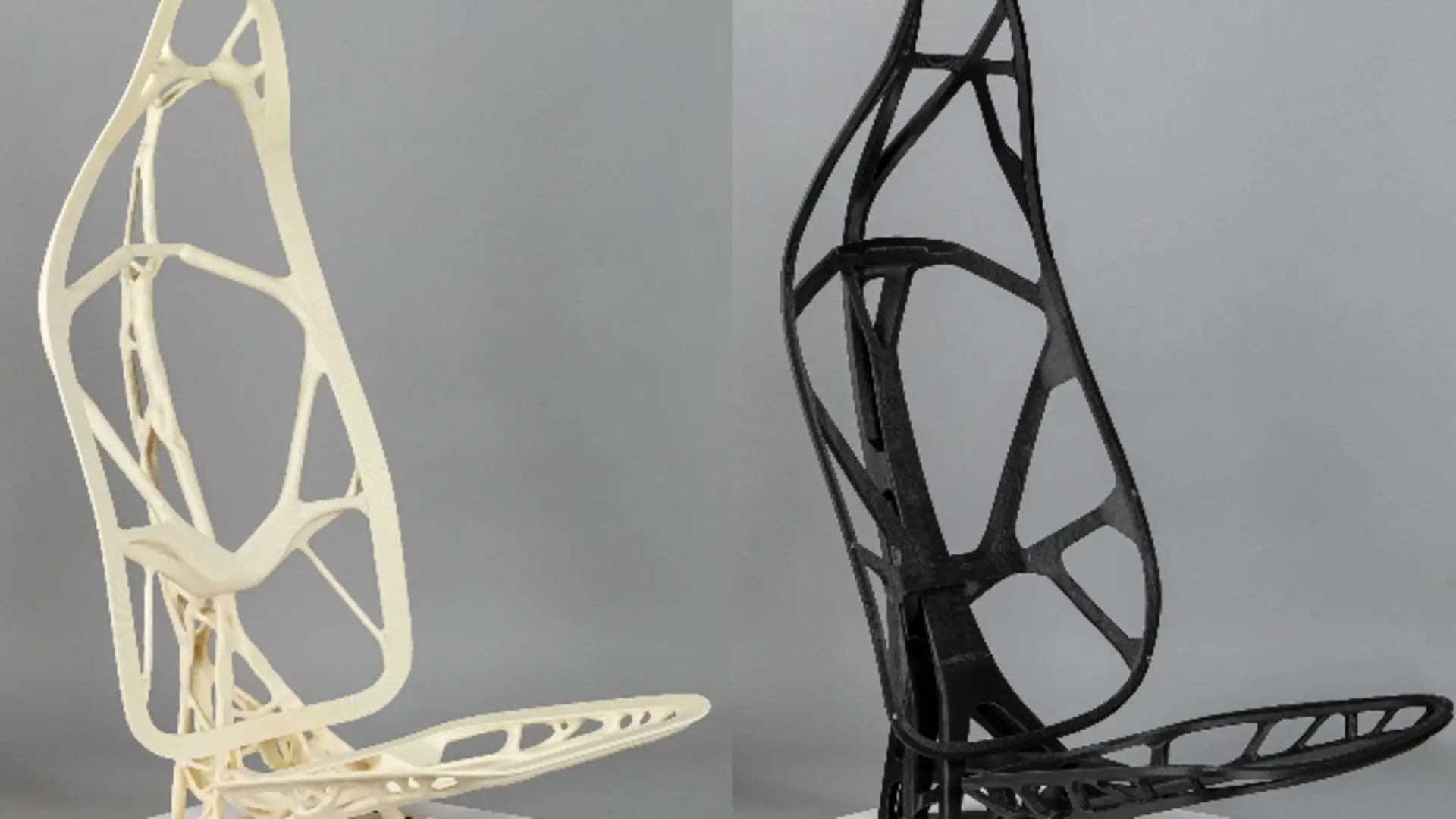
The usual rectangular-shaped seat frame has a flat structure, and the designers tested the idea of optimizing the frame by bringing the core structure towards the center, providing a wider space in front of passengers legs.
Omori says the GD output is « often completely unexpected at first, but we took it further and made slight modifications as we went along. There is always a tradeoff between what a designer wants to do and what generative design creates, and it’s fun to see the various patterns of shapes designers don’t think of ».
Creating this seat frame requires 3D printing, which increases the cost, so further investigation is needed to see that the prototype is compatible with mass-production processes.
Omori notes that with this type of design, it might be possible to keep the spine of the seat the same for various seat sizes and make the rest to fit the user’s physique using a 3D printer, for example. The current seats are made of completely different materials, such as metal frames, urethane, and leather, but Omori says it could be possible to move toward mono-materials with generative design.
Volkswagen
The orange wheel shown here is on a vintage Microbus. It was generated by VW and Autodesk; VW’s Innovation and Engineering Center in California retrofitted an existing bus with an electric drive system, and used generative design to lightweight some of its components—including the wheels, which weigh 18 per cent less than a comparable one conceived more conventionally.
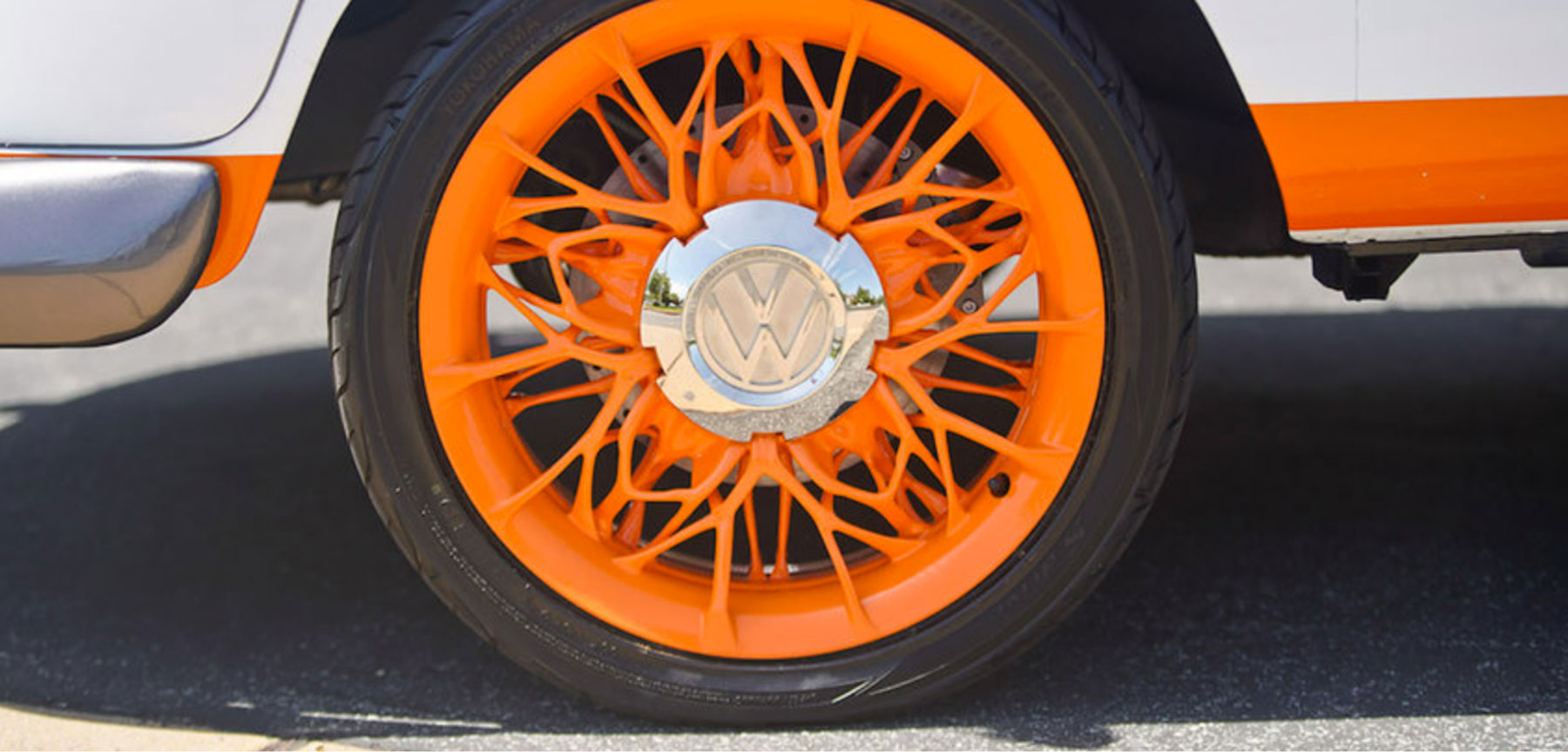
With generative design it is possible to create structures humans might not have thought of, says VW Group Senior Product Designer Andrew Morandi: « One of the biggest surprises for me was seeing just how much material you could remove from a conventional wheel structure ».
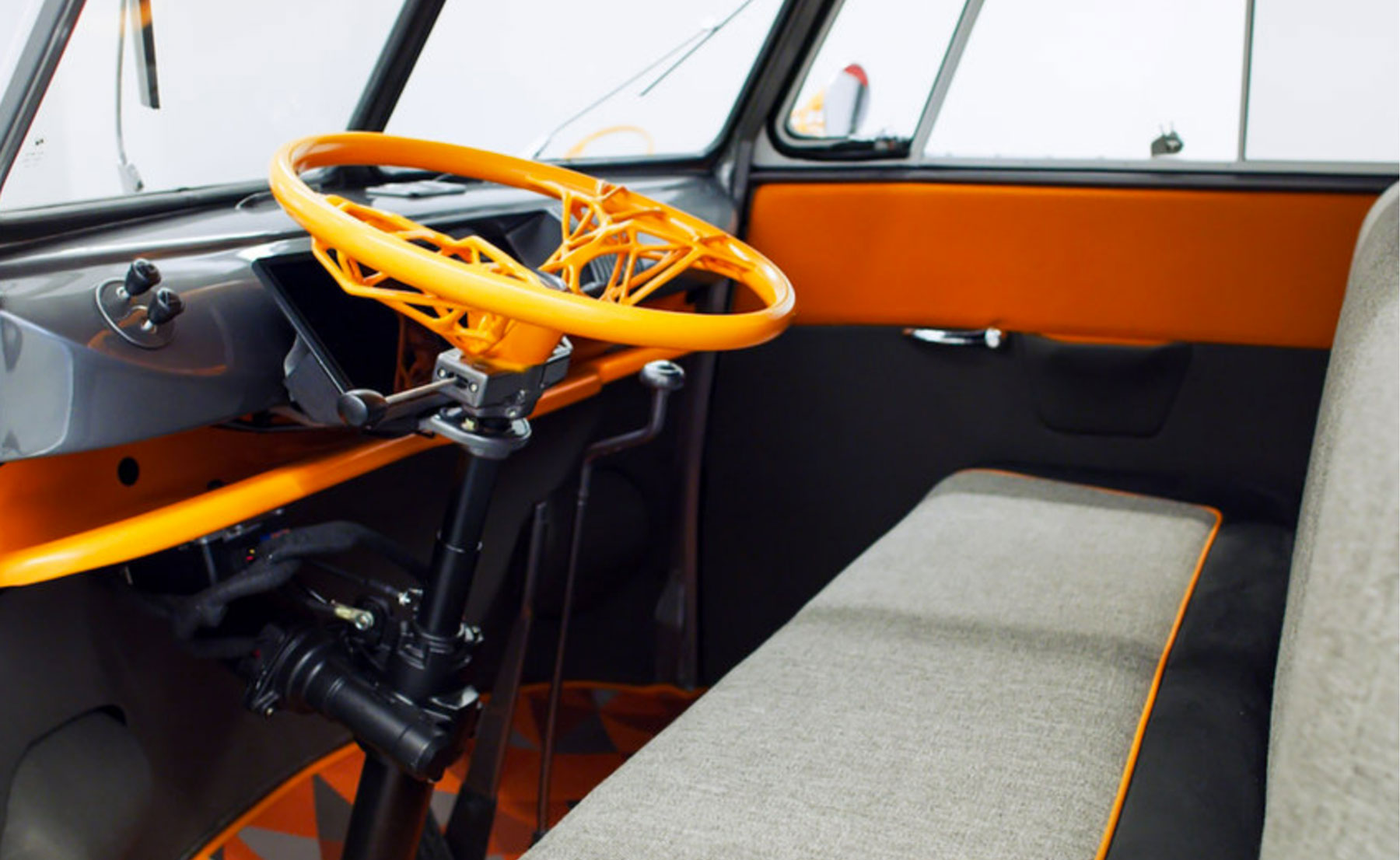
The VW team also applied generative design to the sideview mirror mounts, the steering wheel, and the rear furniture supports shown in these two pictures.
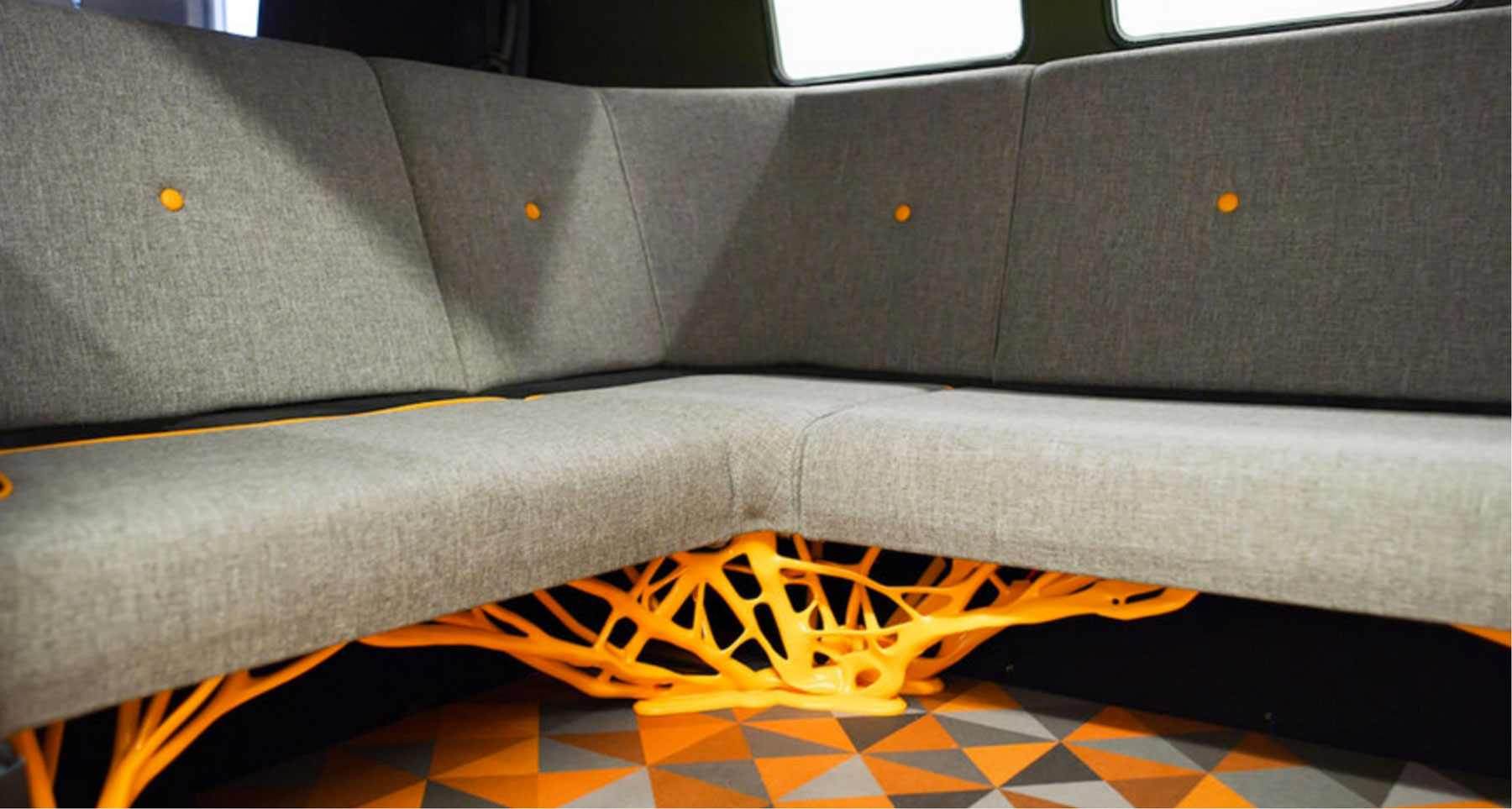
VW Group Principal Product Designer Erik Glaser says, « We wanted to put a generatively-designed object in a place where people will touch it because not only is it intricate and beautiful, but it can also give a sense of just how strong these parts can be ».
BMW
BMW has used generative design to create intricate dashboard skeletons that minimize material usage without compromising structural integrity. This approach ensures that parts like the dashboard are both functional and visually appealing, while maintaining a lightweight structure.
Holger Hamps is President of BMW subsidiary Designworks. His teams are using generative design techniques to design new wheel rims and car seats: « We are feeding both technical parameters and design concepts into the program. It (…) takes into account the different specifications as it creates variants. Artificial intelligence is enabling new approaches to be taken and is only in its infancy in the design process. It already features in our day-to-day communications and is becoming more and more important ». Nevertheless, Hampf says this intellectual and creative input will not be achievable by machines working autonomously in the foreseeable future.
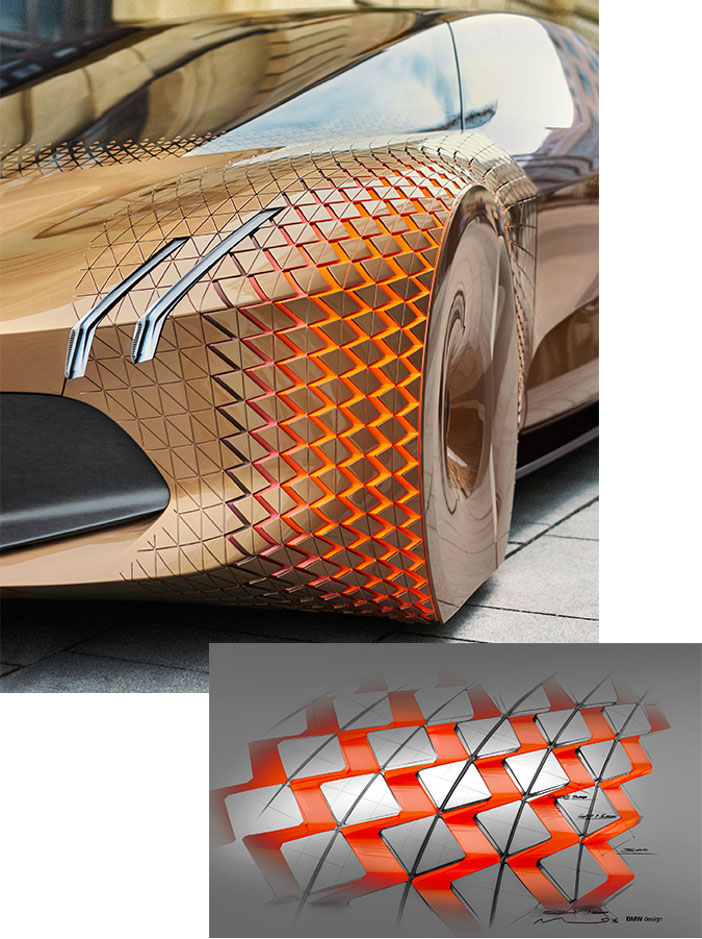
More examples
Hyundai, through partnerships such as with Sundberg-Ferar, is integrating generative design into their vehicle development, particularly for interior elements
Nvidia Omniverse, in collaboration with automakers like BMW, supports the use of generative ‘AI’ in creating exterior components and also user interfaces and interior designs. These tools assist in exploring new textures and materials, improving the user experience of elements like door panels and seats.
Rivian is exploring advanced design tools like generative design to create highly functional, sustainable, and æsthetic interiors for their electric SUVs and trucks. Rivian’s focus on adventure and eco-conscious design makes GD an excellent fit for creating lightweight, modular interior components that align with their brand values of sustainability and durability.
These examples demonstrate enthusiasm in the automotive industry for generative design, but again, the technology and technique are immature; its dependability is still far from proven or presumable. Especially for highly complex designs involving human factors, aesthetics, and large-scale manufacturing, GD still requires a great deal of refinement and human oversight. This will probably remain so for at least another generation of vehicles, at least for everything concerning highly creative tasks requiring skill, talent, and intuition. Perhaps one day an algorithm will be able to replicate those skills with human-like panache…or not; we will have to wait and see!