Car users, particularly in America, are regularly posting videos showing what they describe as a serious design flaw: some headlamps are recessed such that they’re practically guaranteed to scoop and collect snow, which completely occludes the lenses.
He’s got a point: snow is opaque, so snow-packed headlamps won’t light the driver’s way at all. Maybe not such a big deal if it’s just a little light, fluffy, dry snow—the kind that can easily be brushed off before driving, and isn’t as likely to build up while driving. But wetter, heavier snow, ice, and freezing slush can quickly and easily accumulate while driving, nullifying the driver’s vision and spoiling the car’s conspicuity, in weather and road conditions where visibility and conspicuity are especially important. And what of a vehicle parked outside in a storm? Its lights might well be so heavily encrusted that they cannot readily be cleared. Then the driver must choose between unsafe driving and no driving.
And it’s not just passenger cars and light-duty trucks, either; heavy trucks, buses, and other commercial vehicles are at risk, as well—including emergency vehicles which have to be fully ready to safely drive at any moment, even in terrible weather.
Even short of total blockage by opaque snow or frozen slush, ice and frost buildup on lamp lenses can distort the beam, sending light where it shouldn’t be (which causes glare) and away from where it should be (which degrades the ability of people and cameras to see what they must). For many years, it wasn’t much of a problem even with recessed lights; yesterday’s tungsten, halogen, and HID lamps readily self-defrosted, because with those technologies the light and heat are coincident—they both exit together out the front of the lamp. As a result, no regulations developed to require any degree or speed of lens-clearing analogous to the presence and performance requirements for windshield and backglass defoggers; the closest ever to evolve was the old requirement in Scandinavian countries for headlamp wipers—pressure-jet washers would not suffice—and that requirement was quashed in the early-1990s drive to eliminate country-specific lighting requirements throughout Europe (that was when France lost their yellow-headlights requirement and the UK lost their dim-dip requirement).
But with LEDs, it’s different: the light goes forward out the front, but the heat goes rearward. So the lenses run cold, and frost, ice, snow, and slush can adhere and accumulate. There has still been no movement toward a regulation addressing the matter, but it has been under scrutiny. A broad and deep study was done in 2014 in Sweden (naturally!) as a master’s degree thesis, looking at methods of tackling the problem on front and rear lights, and effective ways of testing the performance of frost-up countermeasures.
Even in the absence of regulations, industry has been working to devise solutions, especially for commercial vehicles. During the DVN event last week in Munich, JW Speaker CTO Dragan Popovic spoke on this topic. It’s one he’s well positioned to discuss; Speaker were early to market with LED headlamps for trucks and buses, and they’re headquartered in Wisconsin, which gets some of the United States’ harshest winter driving conditions.
This phenomenon is well known by automakers—for lamps, yes, and also for ADAS sensors. DVN CEO Paul-Henri Matha, when he was working at Volvo Cars, gave a presentation about sensor impairment in winter conditions at the AutoSense event in October 2020, focusing mainly on cameras and radars.
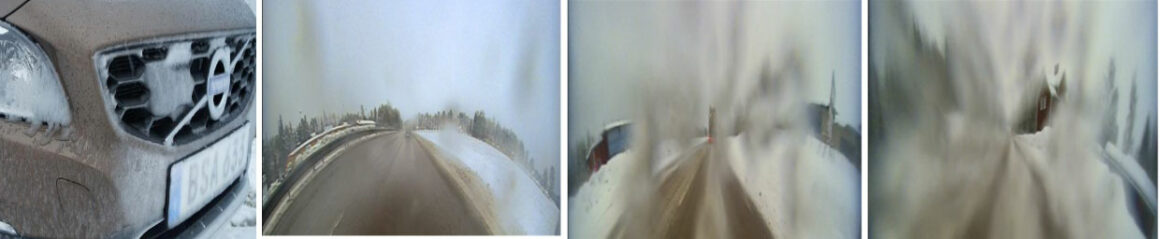
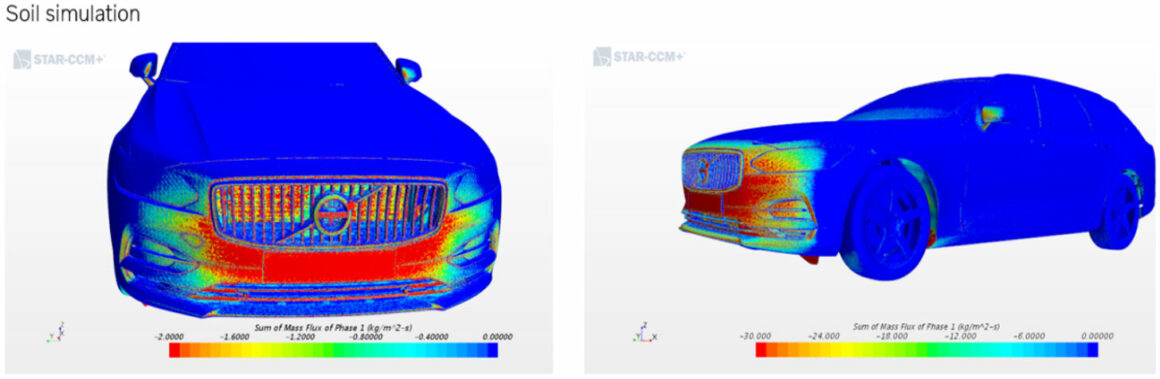
In the false-colour image shown here, the red area signifies sticking snow. In this particular example there is no snow sticking to the lamps, but there is on the bumper and grille, where sensors are often located. Solutions exist for radar integration, as on the Polestar 3 (smart zone with heating element)
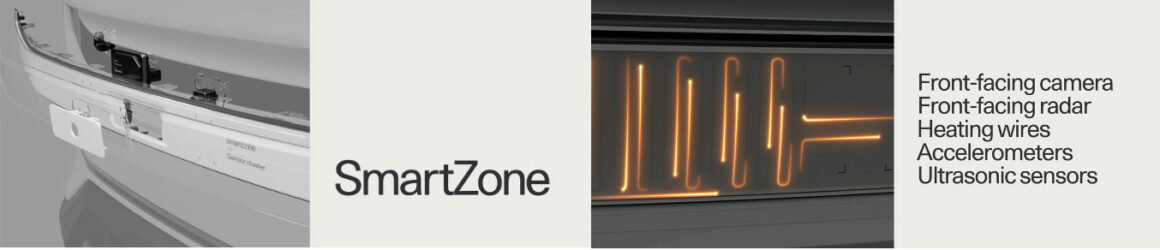
Before LED lamps came along, headlamp outer lens temperature was around 100 °C (depending on the particulars of any given lamp design) and so there was generally not much need for a defrosting solution—indeed, the bigger concern at that time was that heat baking dirt onto the lens!
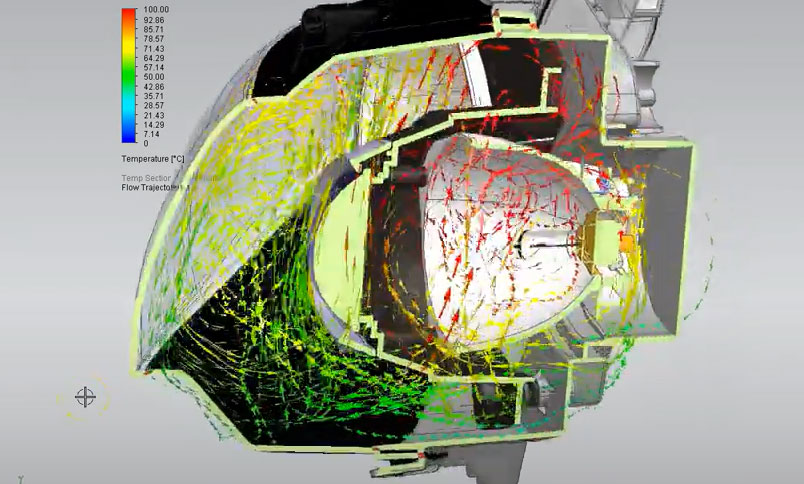
But LED headlamp lenses tend to run at around 40 to 70 °C. Initial solutions were to redistribute heat from the back of the LEDs round to the inside-front of the lamps with air guides, fans, heat pipes, and other suchlike.
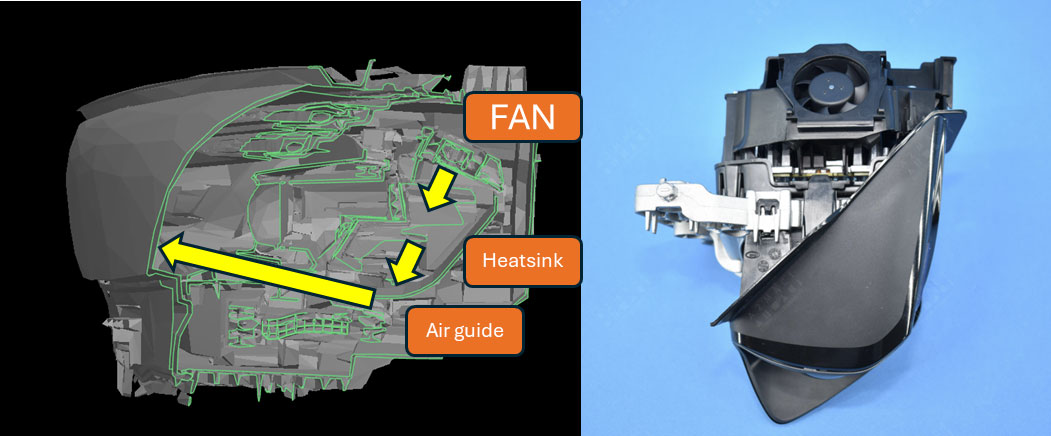
There are multiple reasons why those techniques might not be suitable. For one thing, they might not be enough; LEDs and their associated optical techniques have grown much more efficient since the first LED headlamps, and now good beams can be produced with very low wattage—there very well might not be enough heat anywhere in the headlamp to effectively defrost the lens and keep it clear. So other techniques are being developed and deployed. Heating elements in or near the lens, for example, particularly on trucks in North America.
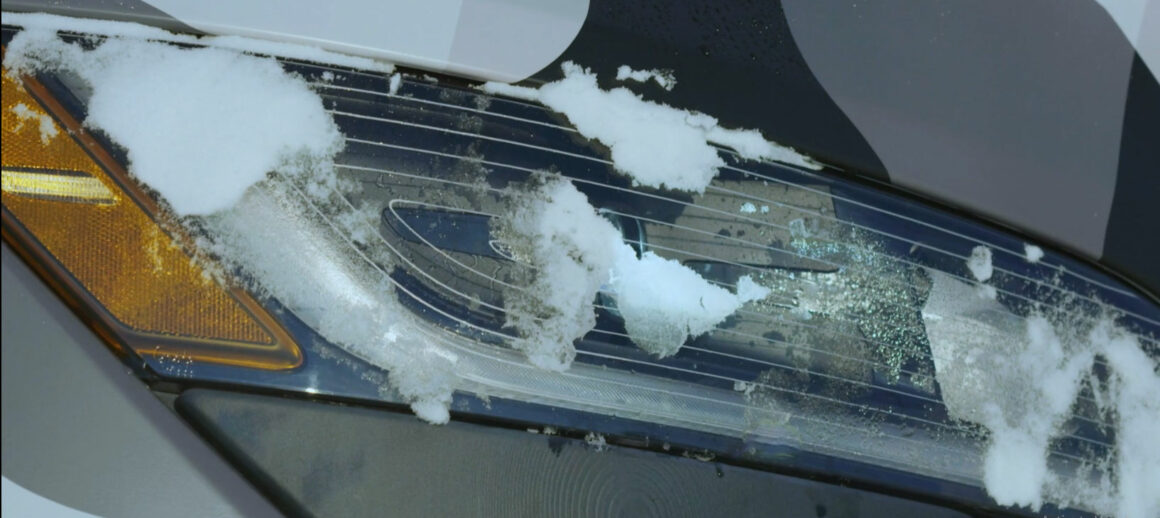
There’s a variety of heating element technologies and techniques.
One of the most common and direct ones involves integrating heating wires within the headlamp lens, as shown here on a truck headlamp.
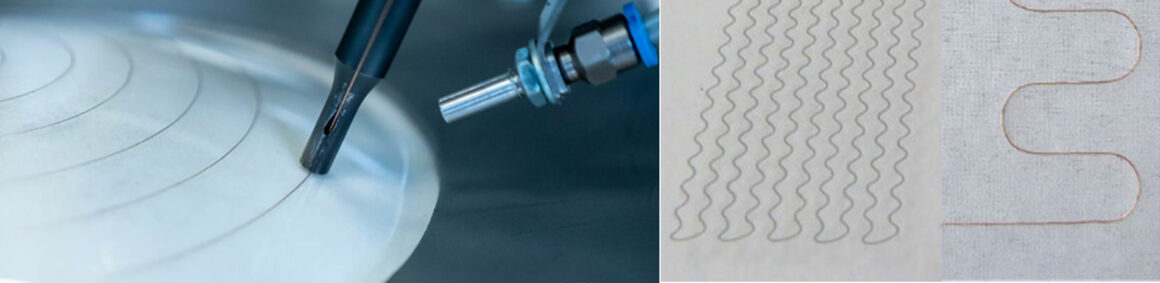
This technology is deployed, for example, by JW Speaker, who call their system Smart Heat. It involves clear films with conductive inks screen-printed on. The 3D film undergoes a thermoforming process after screen printing. Connection to the films is done in the injection mould tool via an insert-moulded PCB: films and PCBs are placed into the moulds. Resin encapsulates the ink and connections during the injection moulding process, for an extremely robust and reliable product. NTC sensors regulate automating de-icing process depending on ambient temperature, and a microLED indicates when heating is active (to facilitate a driver’s pre-trip safety check and continually promote this point of technical excellence).
A million JW Speaker heated-lens lamps are currently in service. The cost is around USD $5 to $7 for a rectangular surface of 150 × 100 mm, with power consumption of about 20W.
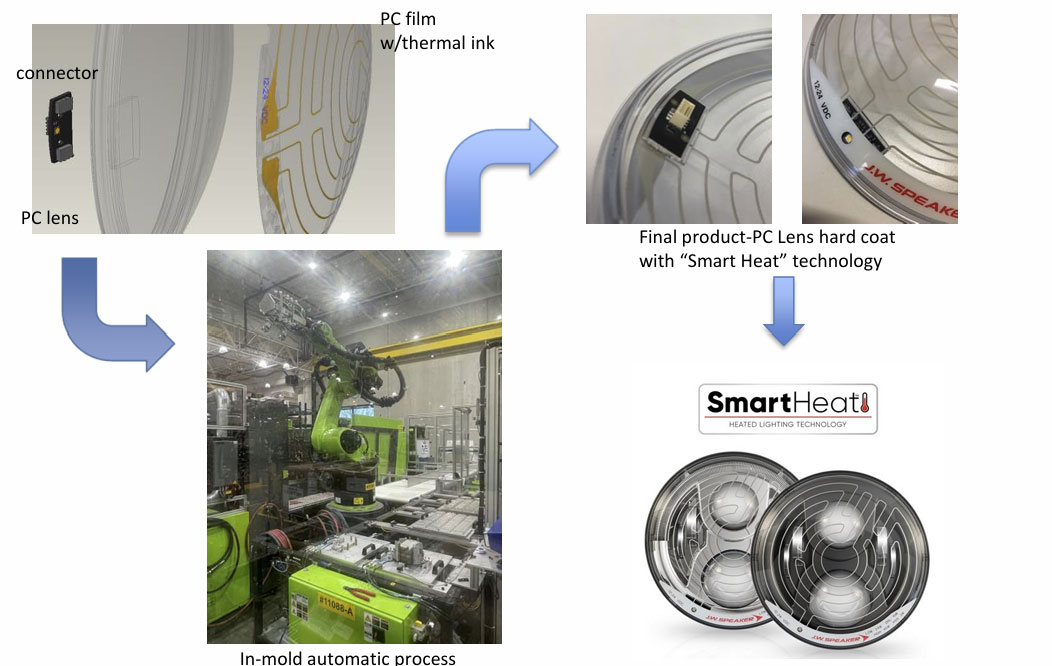
Grote also put this sort of technology on headlamps they supply for trucks like the Freightliner Cascadia, Western Star 49X and 57X, and Mack Granite.
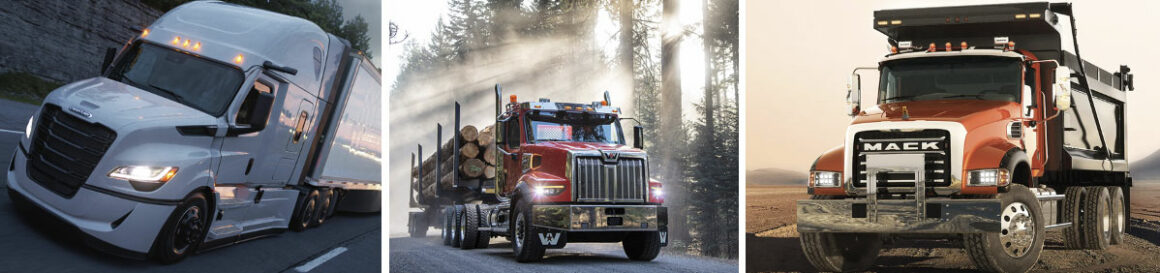
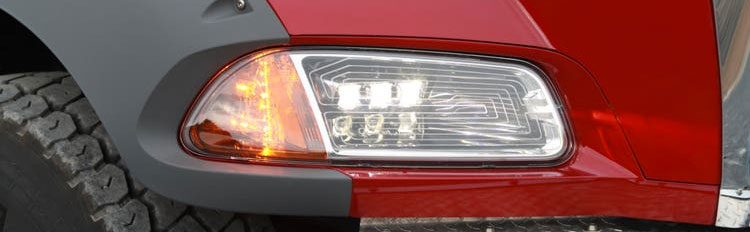
Heating pads are another method of applying heat to defrost lenses and keep them clear. These are typically flexible, thin, and made from conductive materials that can be applied to the internal surface of the headlamp housing—for example, these Hella lamps on Peterbilt 279 and Kennworth T680 trucks (pads are circled with a thin white line in the middle photo here)
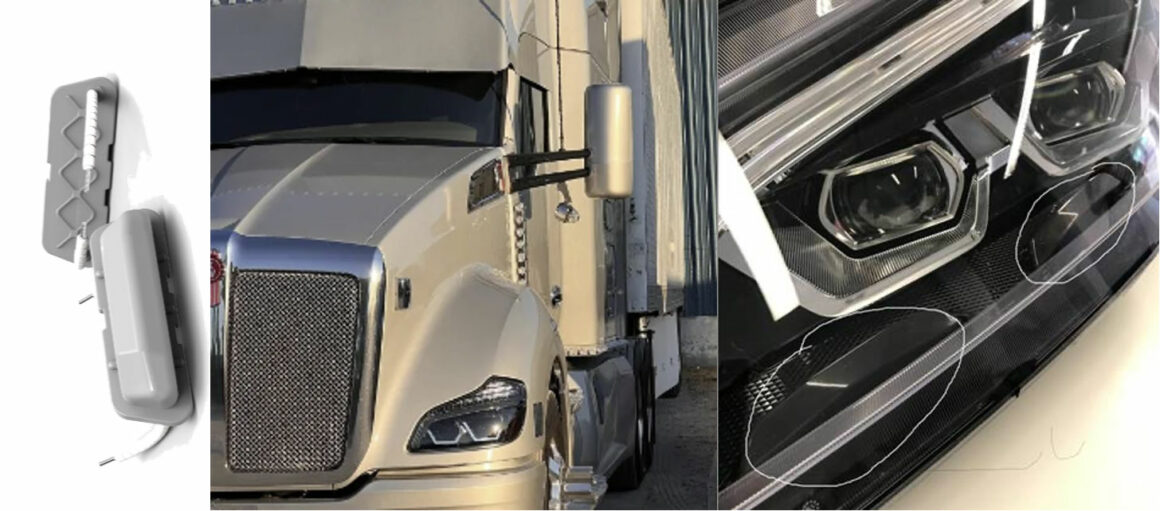
Clear conductive heaters are another line of attack on the problem. Various companies have been innovating in this space with transparent films. One example is Canatu, who use films with carbon nanotubes—one of the best materials there is for thermal conductivity. CNTs are 1,000× more conductive than copper. Applied on a plastic substrate, Canatu’s CNTs form a very thin coating with very small thermal resistance, providing even and power-efficient heating across the whole area. The Canatu film heaters are also energy-efficient, using 40 per cent less energy compared to wire heaters for any given level of heating performance. Such a film heater can be 3D formed before integration. The material is highly stretchable (>200 per cent) and can be bent to a radius of just 1 mm. Film heaters using Canatu CNTs can be thermoformed or high-pressure formed into any 3D shape, offering design freedom for complex geometries. They can be seamlessly integrated into a headlamp’s plastic cover lens through film insert molding. For glass lenses, the heater can be sandwiched between interlayers and laminated between the B- and C-surfaces, or it can be laminated behind the glass on the D-surface.

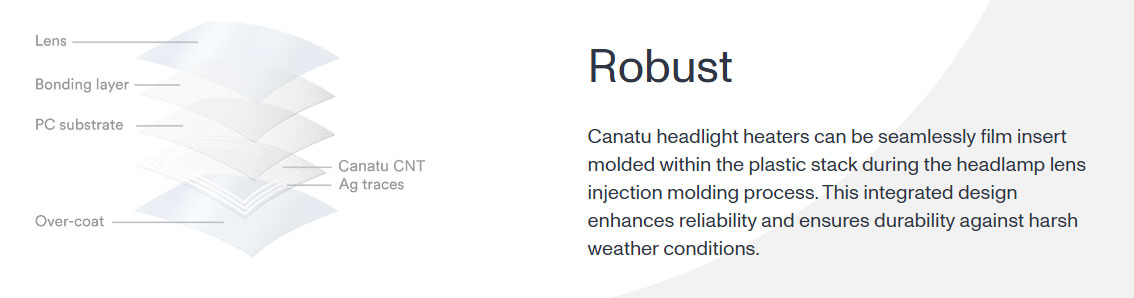
Dupont‘sC3 nanooffering uses silver nanowires for transparent conductive films, inks, and coatings. This enables transparent heating for headlamps and lidar-radar-camera sensors (as well as smart surfaces, EMI shielding, and IR reflection).
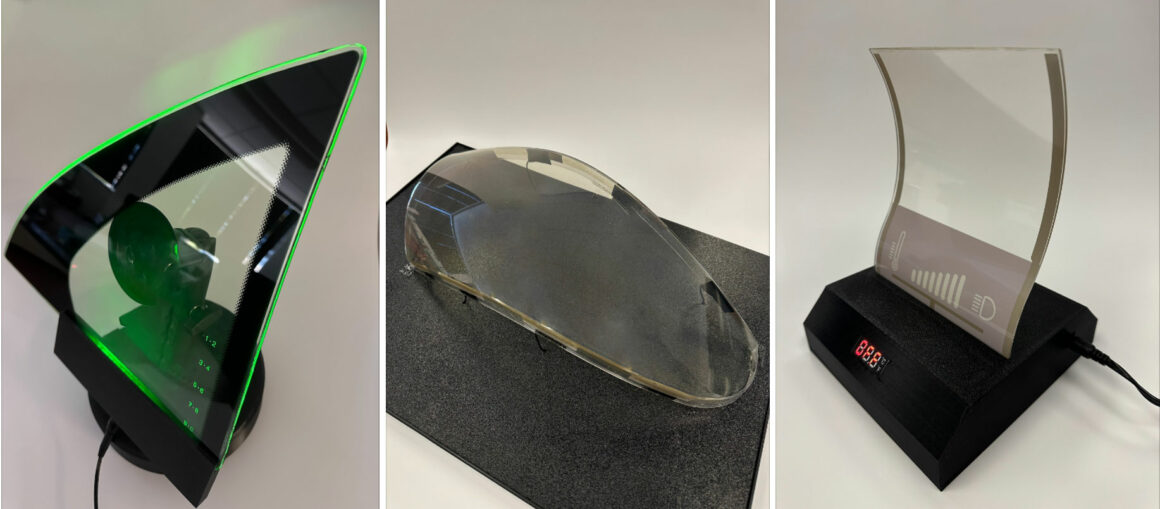
A lidar heater application of this technology will start production this year; the headlamp application target is 2026-2027.