With one of our recent newsletters, we introduced the latest changes to the ESPR regulation, which originally called for a 25-per-cent recycled plastic content for newly developed vehicles.
The proposal has been adjusted to drop that figure to 20 per cent and expand the resources from which recycled plastic can be obtained to count toward the figure by adding the possibility to use pre- and post-consumer waste, including also bioplastics.
The other important change is in the percentage of recycled materials which has to come for end-of-life vehicles, originally set at 25 per cent and now reduced to just 15. That will make it easier for automakers to comply with the regulation, and reduce pressure on the supply chain. The previous targets posed difficulty in sourcing recycled materials from end-of-life vehicles.
But industry associations have raised concerns with the new proposal, saying the weakened goals could have a negative impact on the circularity of the automotive sector and create a false perception of progress.
A joint statement by plastic and environmental associations says, « Ambitious recycled-content benchmarks are crucial to stimulate investments in the technologies and infrastructure necessary to recycle ELVs’ plastics efficiently, enhancing material recovery rates and reducing the volume of waste sent to energy recovery or landfills ».
So, who is right? What’s the compromise between striving for circularity and not worsening things in the automotive industry? Might we need a plastic-free interior…?
Most of the plastic in vehicles can be found in interior trim. And developing a car interior with less plastic is a challenge. The recent proposal allowing to add bioplastic, pre- and post-consumerrecycled content, is surely a good help in achieving the ESPR targets and a sustainable car interior.
Introducing more non-plastic bio-based materials is also a great way to develop sustainable car interiors, but doesn’t solve the short-term issue of having to limit the plastic waste from ELVs and consumers. Therefore, beside the obvious demand for plastic because of its great properties, when we talk about environmentally sustainable interiors,we still think mainly in terms of plastic-waste recycling or bio based plastics, and that’s why regulations are centered around this point.
Bioplastics
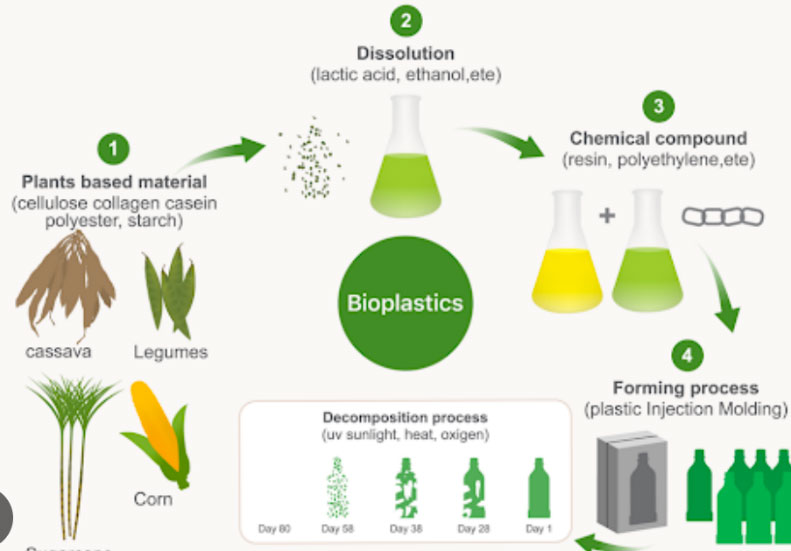
Bioplastics are polymeric materials that can be recycled and readily decomposed (if they’re biodegradable) when they end up in landfills, can replace conventional petrochemical plastics, and are considered superior polymers compared to synthetic plastics due to their biocompatibility, making them ideal for automobile applications.
Main types and applications:
Polyamides (Bio-PA)
Bio-PA is most made from castor oils and sugar cane, and is used in many applications like connectors, brake hoses, fuel lines, and flexible tubing.
Polylactic Acid (PLA)
PLA is produced by fermentation of sugar derived from sugar beet, sugarcane, or corn. It is highly suitable for interior accessories like mats, carpeting, upholstery, consoles.
Polypropylene (Bio-PP)
Bio-PP is made out of sugarcane and can be implemented to substitute synthetic plastics in the production of body panels, dashboards, door pockets and panels, consoles, and ventilation/air conditioning parts.
Corn and sugar cane are the most effective feedstock for bioplastic manufacturing, ensuring the highest yields and the least land area to grow.
Along with the obvious point of bio-based materials helping to achieve a sustainable interior design, there are two more worthy advantages:
For ELVs, the non-recyclable plastic material known as shredder residue ends up in landfills and contains hazardous chemicals like lead, cadmium, polychlorinated biphenyls (PCBs), and more. Using bio-based and biodegradable material seems a promising solution to overcome the pollution caused by landfill plastic; suvh materials readily decompos if composting temperature are high enough to allows microbes to break them down.
And bioplastics are normally lighter than petroplastics, helping to lower the weight of vehicles and consequently reducing carbon footprint.
Certain challenges are presently slowing down the use of bioplastics:
- Low production; bioplastics represent only roughly 0.5 per cent of the almost 414 million tonnes of plastics produced annually

- Immiscibility; we can’t mix bioplastics with fossil-based traditional plastics, so there is a great need to create a proper supply chain and recycling system for bioplastics.|
- Particular treatment requirements: Biodegradable plastic waste requires certain prevailing environmental conditions to fully decompose naturally, without which we regress to a linear economy instead of circular.
- Supply chain traceability is mandatory, to ensure that bioplastic products align with stringent automotive regulations and help the their end-of-life management . The data collected through traceability initiatives can also support innovation, leading to improvements in bioplastic materials and production technologies.
And there are some outright negative aspects of bioplastics to consider. Reflexively, you might think one of them is that bioplastics are expensive. But is that still true? They use resources called second-generation feedstock, instead of fossil resources. Recently, the price of fossil fuels have fluctuated a lot, and the cost of the bioplastics have been more predictable, though not always comparable to fossil-based plastic. But some OEMs are making allowances for suppliers to slightly increase the cost of their materials, when bio-based.
There’s a lack of experience regarding the ageing behavior and long-term durability of the polymers. Lots of studies on the topic, but for some bioplastics we are still lacking long term data collection to be able to rule out issues on this front.
Probablythe biggest question is whether bioplastic is actually environmentally friendly. Where were its feedstuffs grown, taking how much land and how much water? There are countless studies on the topic, but there’s no clear answer yet.
To minimize the issues, some companies are experimenting with combinations of bio-based and recycled materials. An example is Simax’s innovative naturally-inspired material range. Through special finishes and embossing, polymers from this range can simulate natural effects such as stone, marble, granite, fabric, wood, or a starry sky. Depending on customer specifications and their CO2 reduction goals during the product’s lifecycle, post-consumer and bio-based materials can be included in the formulation, in different percentages.

Sirmax has developed a recycled plastic door panel material to address problems related to the maintenance of mechanical properties, unwanted odors, and the presence of volatile organic compounds on the surface of interior finishes. The Italian company has formulated a polypropylene with 5 per cent talc added. It contains 30 per cent recycled material derived from post-consumer waste (dumpster waste). This compound from the Green Isofil family resembles the mechanical and aesthetic characteristics of virgin plastic, offering a valid alternative. The Sirmax-branded door panel retains impact- and scratch-resistant properties, resolves stickiness and odor, and, most importantly, its carbon footprint is reduced by up to 21 per cent compared to virgin raw material. This solution can also be applied to other car parts, like the glove compartment and center console.
The innovative Sirmax material family includes Green Isofil (polypropylene with mineral filler, formulated with waste plastics), NewPlen (recycled polypropylene for injection molding, extrusion, and thermoforming), and NewTen (recycled high-density polyethylene for extrusion and blow-molding).
Food waste as a resource
A possible alternative solution to plastic comes from researcher investigating, as possible biomaterials, household waste like coffee pulp, eggshells, red lentils, walnuts, and rice. These combine the two fundamental requirements of regulations: using bio sources and using pre-post-consumer waste (even if not plastic waste).If they become widespread, they could lead toward plastic-free interiors.
While materials like cotton, hemp, and wool are already largely used for seating, headliners, and door panel bolsters as natural soft-trim alternatives to fossil-based textiles, recycled food waste is still not present as a standard material. But it is certainly a promising alternative to be further explored.
One company doing so is Callum Design,who worked together with green-tech Ottan to determine the most appropriate materials capable of replacing plastics yet still meeting the rigorous design, environmental and engineering requirements of a car. The solutions they found include:
- eggshells mixed with resin to create a smooth, opaque material with either a glossy or matte surface. Application examples include the trim surround for the window switches. If walnut shells are added to the eggshells, it increases the recycled content from 78 to 84 per cent.
- rice or lentils can be turned into a smooth, translucent material ideal for illuminated areas of the car such as lamp covers or illuminated switches.
- coffee pulp, with its flame-resistant properties, could replace traditional plastics for glossy, decorative trim such as dashboard inserts.
- to demonstrate that sustainable materials can still offer vivid colors, Callum identified purple carrot pulp which provides a mulberry-like color for trim parts.
- tree leavescan be recycled on a dark, smooth surface offering an alternativenatural finish to wood veneers for the center console or dashboard.
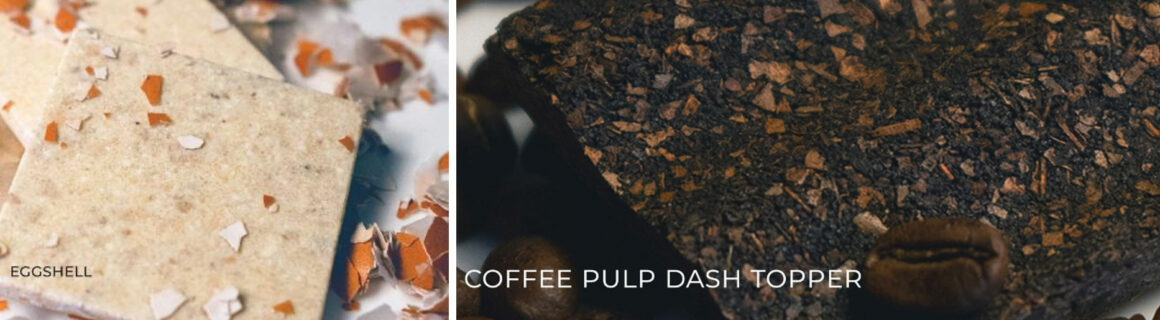
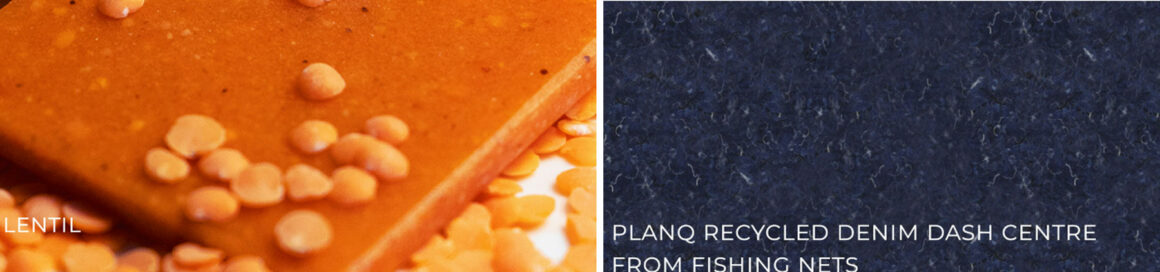
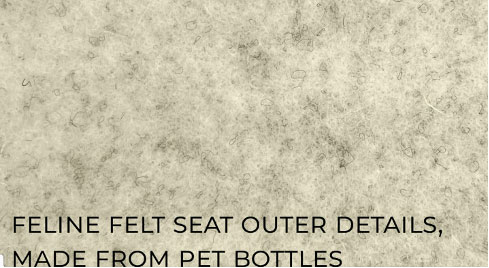
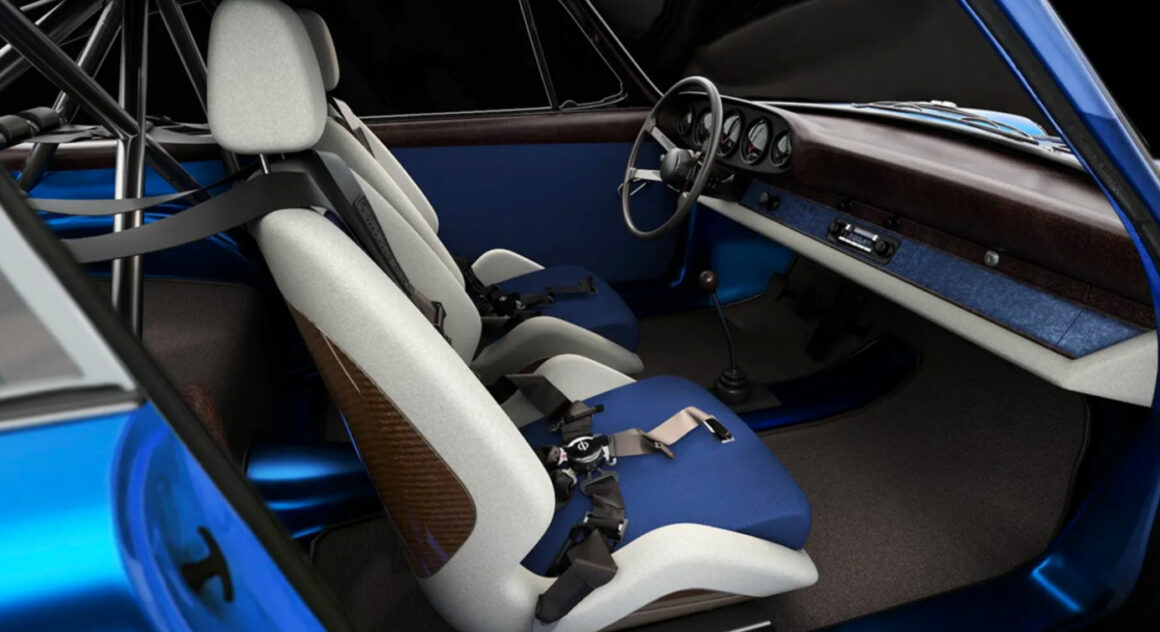
Moving on to the other target, the use of pre- and post-recycled materials. Can this make a big difference in terms of circular economy efficiency?
Pre-consumer recycled content is made out of manufacturer waste that never actually reached the consumer or transforming industry for one reason or another—scraps, rejects, trimmings—and that is normally already repurposed from companies itself into something new rather than trashed.
Post-consumer content is likely to end up in landfills or, most probably, in our oceans. So of course it is preferable to pre-consumer content, but in case of automotive materials, it might be also more expensive because of the recycling process and the supply chain needed to circulate it back into automotive components.
Recycled content is today mainly used in hidden parts of the car, mainly because of aesthetic appearance not meeting requirements.
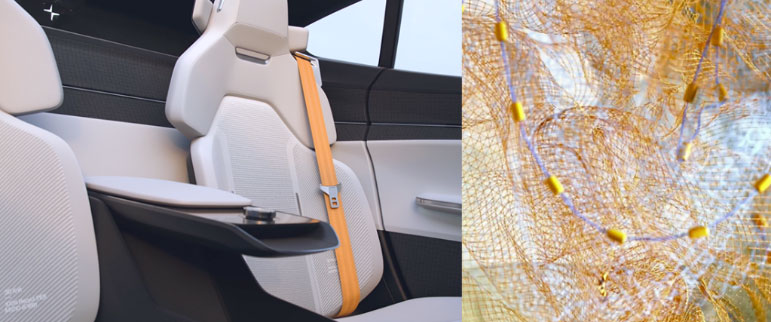
So, how can we increase the percentage of recycled materials for visible interior components, without compromising aesthetic and performance? Many examples of innovative car makers show that it is not difficult, but it requires a shift in thinking about the window of acceptance, both from the technical (harder) and the aesthetic (easier) standpoints.
Increasing the use of recycled plastic is linked to the balance between of performance, appearance, and comfort, and research is helping to pave the way. A Spanish institute, AIMPLAS (the Plastics Technology Centre), has launched a project called SURFTOP, financed by EU as well, to study the quality of recycled plastics from automotive waste.
The surface properties of plastics refer to the material’s surface characteristics, which can affect its appearance (gloss, color, roughness), its bonding capacity (especially for parts that will be painted), and its resistance to wear, impact, scratching, and chemical agents. Inside the vehicle, it is necessary to guarantee low emissions of volatile organic compounds (VOCs) and odors from recycled plastic materials to comply with the requirements of manufacturers.
The project focuses on studying the effects of using recycled material to manufacture parts for the interior and exterior of vehicles and aims to establish and develop technologies that make it possible to comply with vehicle interior air quality (IAQ) requirements while maintaining the surface properties established by manufacturers.
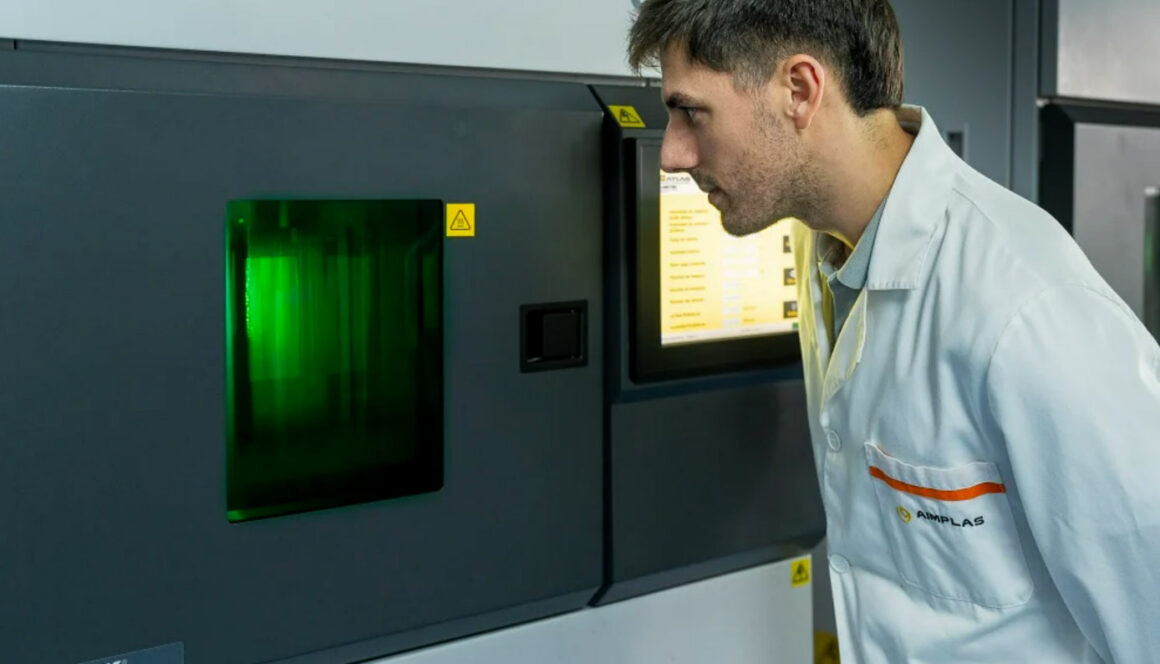
This project also involves Prisma Soporte Industrial, a company specializing in injection molding and painting of automotive parts, which will help validating the process and functionality of the recycled materials.
So, it looks like OEMs will have soon a bigger choice of tested recycled materials at hand. Designers stand to gain from the results of this study, by counting on a larger range of options to select their preferred surfaces.